After the oil spills onto the water surface, it will rapidly spread and drift under the influence of its own gravity, wind, current and other factors. Therefore, the primary task of the emergency response to oil spill is to take effective measures as soon as possible to control the oil spill and prevent its further spread and drift, in order to reduce the pollution range of the water area and alleviate the degree of pollution damage. The measures taken to control the oil spill within a smaller area and prevent its further spread and drift are called oil spill containment.
In the event of an oil spill accident, appropriate containment measures and containment equipment and materials should be adopted according to the actual situation. The equipment and materials that can be used for oil spill containment include natural resources and industrial manufactured products. Natural resources include corn stalks, straw and logs, etc.; industrial manufactured products include oil containment booms, ropes and nets, etc. This chapter mainly introduces oil containment booms.
At present, there are quite a variety of types of oil containment booms in the market. The transportation industry standard of the People’s Republic of China – Oil Containment Boom (JT/T2022-2001, hereinafter referred to as “Oil Containment Boom Standard”) classifies oil containment booms as:
1. Solid floatation boom
2. Fence boom
3. External tension boom
4. Inflatable boom
5. Shore seal boom
6. Fire resistant boom
In the IMO “Model Text for Oil Spill Emergency Training”, the oil booms are classified into three types, namely curtain-type oil booms, fence-type oil booms and beach-type oil booms. This chapter introduces the oil booms in accordance with the classification in the IMO “Model Text for Oil Spill Emergency Training”.
The structures and uses of different types of oil booms are not the same. According to the actual situation, choosing the appropriate oil boom and adopting reasonable deployment forms can truly exert the functions of the oil boom and achieve the purpose of oil spill containment and recovery.
Section 1: The function and structural features of the oil barrier.
1. The functions of oil boom
The functions of oil booms can be summarized as three main ones: containment and concentration, oil spill diversion and prevention of potential oil spills.
1.1 Containment and concentration of oil spills
After an oil spill accident occurs, the oil spill will rapidly spread and drift under the influence of power flow, wind and other external factors, forming a large contaminated area. When an oil spill occurs in open waters, nearshore waters or ports, timely setting up oil barriers can promptly control the spreading oil spill. By dragging the oil barriers or reducing the surrounding area, the oil film can be gathered in a smaller area for recovery. This not only prevents the spread of the oil spill but also increases the thickness of the oil film, facilitating recovery or other treatments, as shown in Figure 3-1.
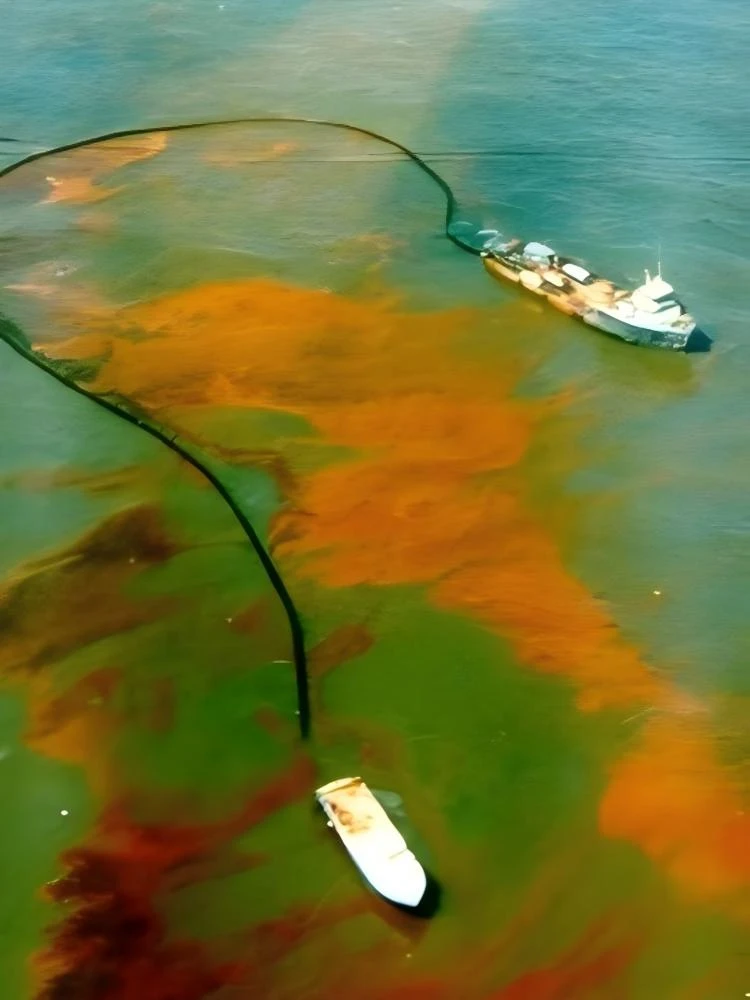
(3-1 Containment and concentration of oil spill)
1.2 Oil spill diversion
After an oil spill accident occurs, under the influence of external factors, the spilled oil will drift and spread at will. To facilitate the recovery operation or to guide the spilled oil to the designated location, especially in rivers or areas with rapid current near the shore, to effectively control the flow direction of the spilled oil for easy recovery or to prevent the spilled oil from entering sensitive areas, oil barriers are usually set up at a specified Angle for prevention. There are generally two situations for oil spill diversion. One approach is to use long-term oil barriers for placement, typically at water intake points and power plants, etc. Another situation is to temporarily set up oil barriers. This is mainly when an oil spill occurs. According to the specific circumstances, oil barriers are temporarily set up to achieve the diversion of the spilled oil and direct it to areas that are easy to recover or other non-sensitive resource areas, as shown in Figure 3-2.
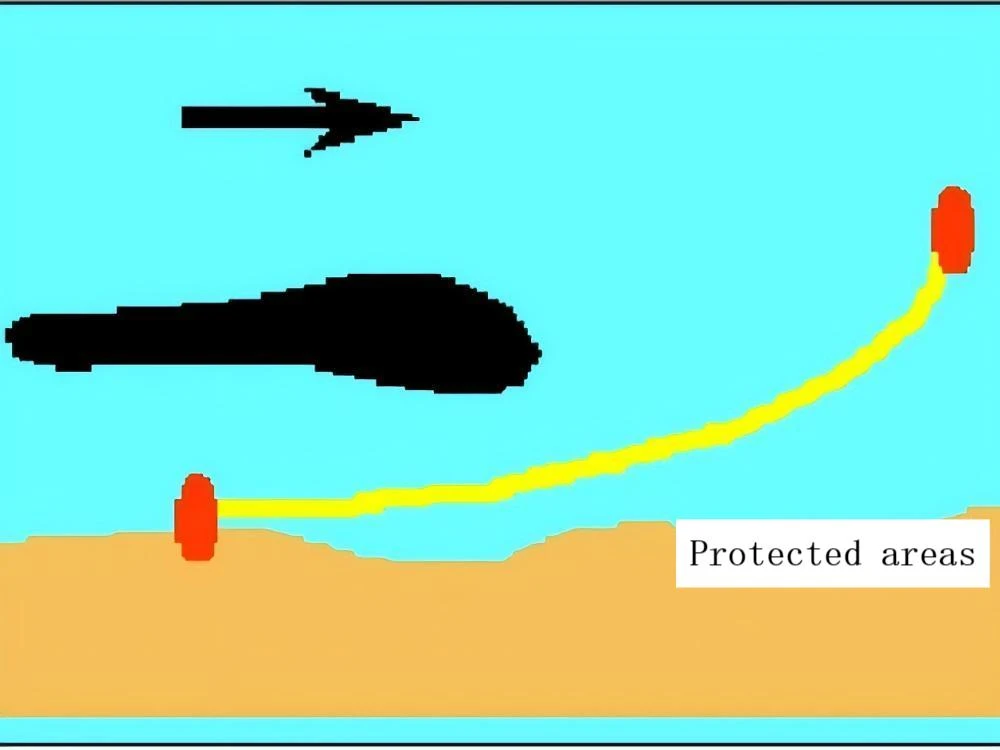
(3-2 Oil spill diversion)
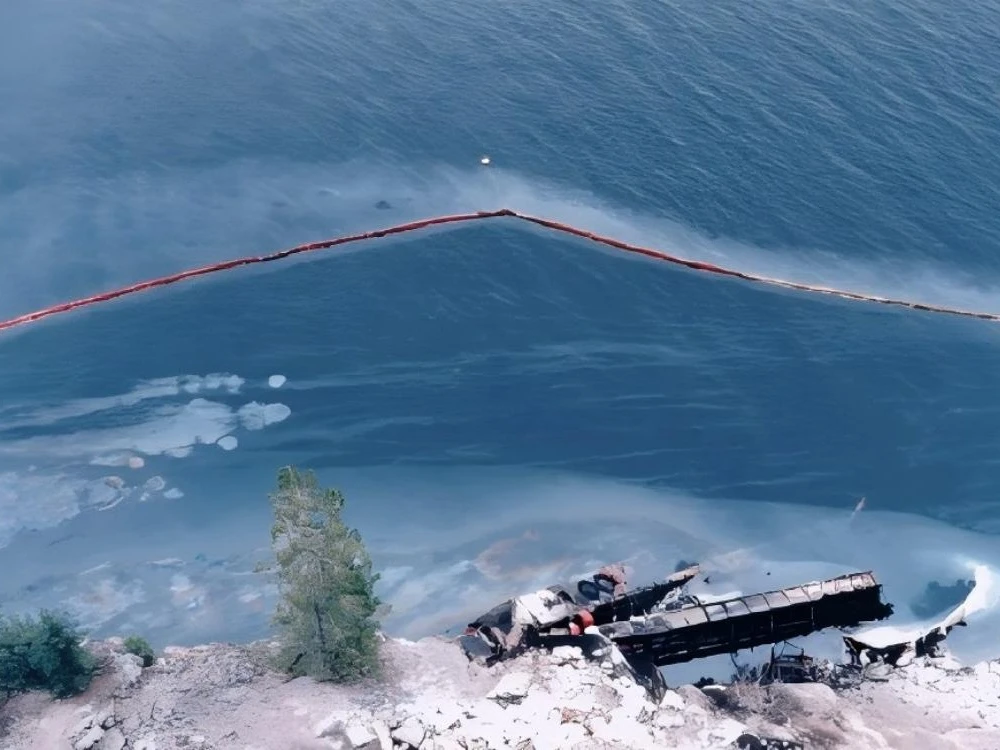
(3-3 Preventing potential oil spills from stranded ships)
1.3 Prevent potential oil spills
Preventing potential oil spills usually refers to setting up oil barriers in advance in areas where oil spills may occur or where there is a risk of oil spills, based on the local water conditions, for oil spill prevention and control. This way when an oil spill actually occurs, it can prevent the spread of the oil spill, so that recovery measures can be taken to recover the oil spill in the containment in a timely manner. When ships carry out oil loading and unloading operations at the wharf or oil transshipment at the anchorage, they usually need to set up oil barriers in advance in accordance with the prescribed requirements for control. Sometimes, for stranded or sunken ships, appropriate containment should also be carried out according to the actual situation before they are salvaged, as shown in Figure 3-3.
2. Structure and Performance Indicators of the oil barrier
At present, there are many manufacturers of oil booms in the world, and there are also many types and forms of oil booms. Despite this, the basic structure of the oil booms is largely similar, basically consisting of a floating body, a skirt body, tension bands, counterweights and joints.
- Floating body: The part that provides buoyancy for the oil barrier. Its function is to use air or buoyancy materials to provide buoyancy for the oil barrier, enabling it to float on the water surface. The floating body can be placed inside the surface layer of the oil barrier or outside the surface layer.
- Skirt body: Refers to the continuous part of the oil barrier below the floating body. Its function is to prevent or reduce the escape of oil from beneath the oil barrier.
- Tension band: It refers to a long band component (chain, belt) that can withstand the horizontal tensile force applied to the oil barrier. It is mainly used to withstand the pulling force generated by wind, waves, tidal currents and dragging.
- Counterweight: A ballast that enables the oil barrier to droop and improves its performance. It can keep the oil barrier in an ideal state in water. It is generally made of steel or lead materials, or water is used as the ballast.
- Joint: A device permanently attached to the oil barrier and used to connect each section of the oil barrier or other auxiliary facilities.
The performance indicators of the oil barrier generally refer to the freeboard, draft, height, total height, weight, total buoyancy, buoyancy ratio and tensile strength of the oil barrier.
- Freeboard: The minimum vertical height above the waterline of the oil barrier. Used to prevent or reduce the splashing of oil from above the oil barrier.
Draft: The minimum vertical depth of the surface layer below the water line of the oil enclosure. - Height: The sum of the free board and draft of the oil barrier.
Total height: The maximum vertical height of the oil barrier. - Weight: The total weight of a fully assembled section of the oil barrier, including the joint of the oil barrier.
- Total buoyancy: The weight of fresh water displaced when the oil barrier is completely submerged in water.
- Total buoyancy ratio: The ratio of the total buoyancy to the total weight of the oil barrier, commonly referred to as the buoyancy ratio. A high buoyancy ratio indicates that the oil barrier has a strong ability to return to a floating state after being submerged by water. This self-recovery ability of the oil barrier is called wave-following property. The higher the buoyancy ratio is, the stronger the self-recovery ability is and the better the wave following performance is.
- Tensile strength: The breaking force at which the oil barrier breaks under tension.
3. Basic Components and Characteristics of the Oil Barrier
3.1 Curtain-type oil barrier
The basic components of the curtain-type oil boom include the float, skirt, tensioning device, ballast and joint, etc., as shown in Figure 3-4. According to the type of float material, curtain-type oil booms can be divided into inflatable oil booms and solid float oil booms.
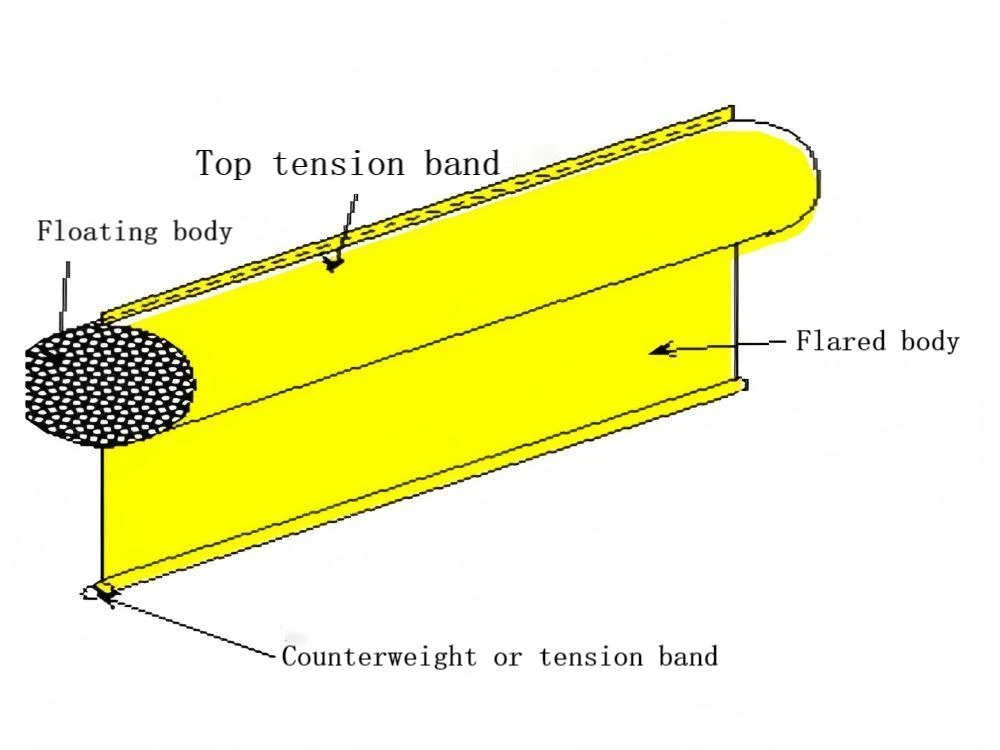
(3-4 The basic structure diagram of the curtain-type oil barrier)
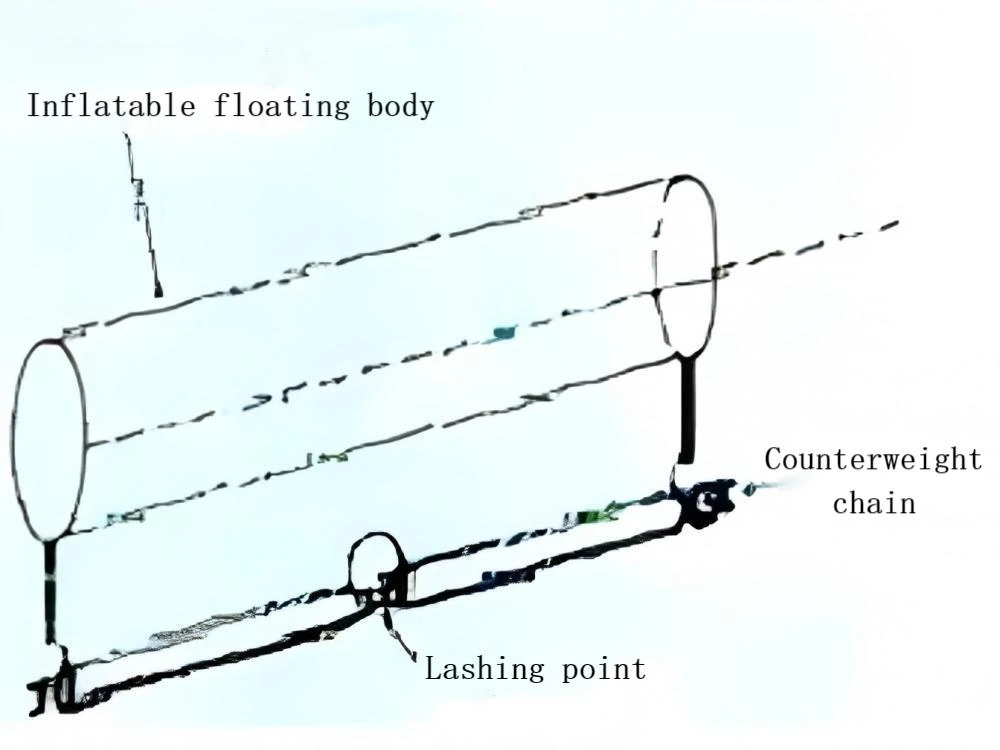
(3-5 The structure of the pressure-inflatable oil barrier)
(1) A curtain-type oil barrier with an inflatable floating body is called an inflatable oil barrier. According to the inflation method, inflatable oil booms can be further classified into pressure-inflatable ones (see Figure 3-5) and self-inflatable ones (see Figure 3-6). According to the structure of the air chamber, inflatable fuel booms can be further classified into single-air chamber fuel booms and multi-air chamber (the length of each air chamber is approximately 2 to 4 meters) fuel booms. At present, the inflatable oil booms produced domestically are generally multi-chamber. From the actual situation, the multi-air chamber oil barrier has a better floating ability. Even if one of the air chambers is damaged, the entire oil barrier will not sink as a result, and thus it is more widely used.
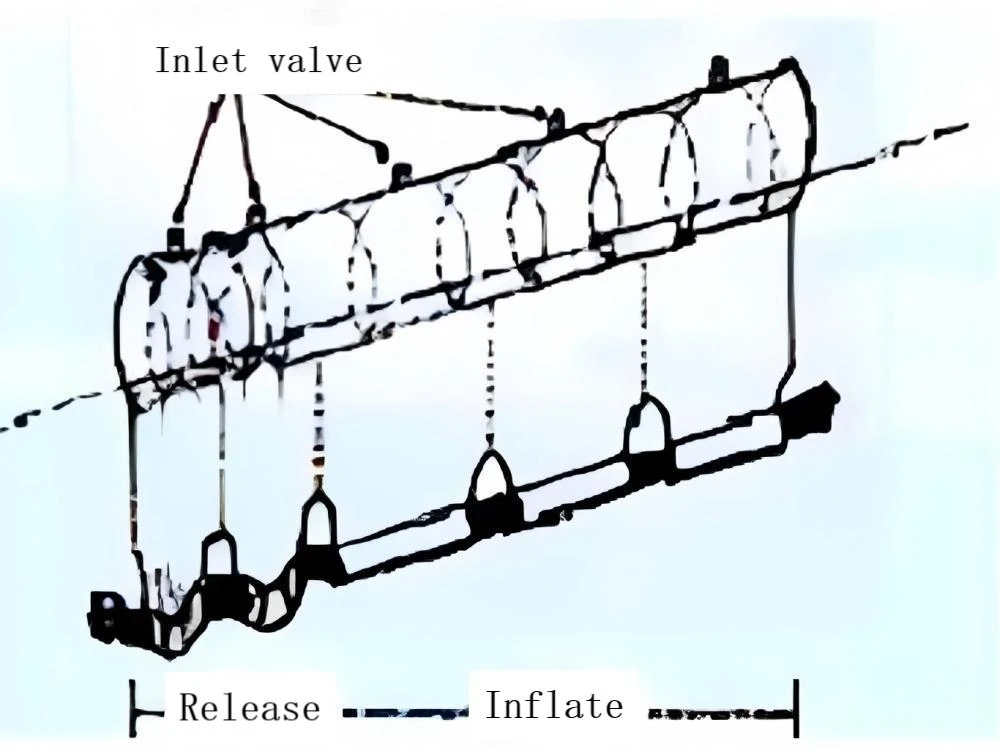
(3-6 Structure of Self-Inflating Oil-Fighting Netting)
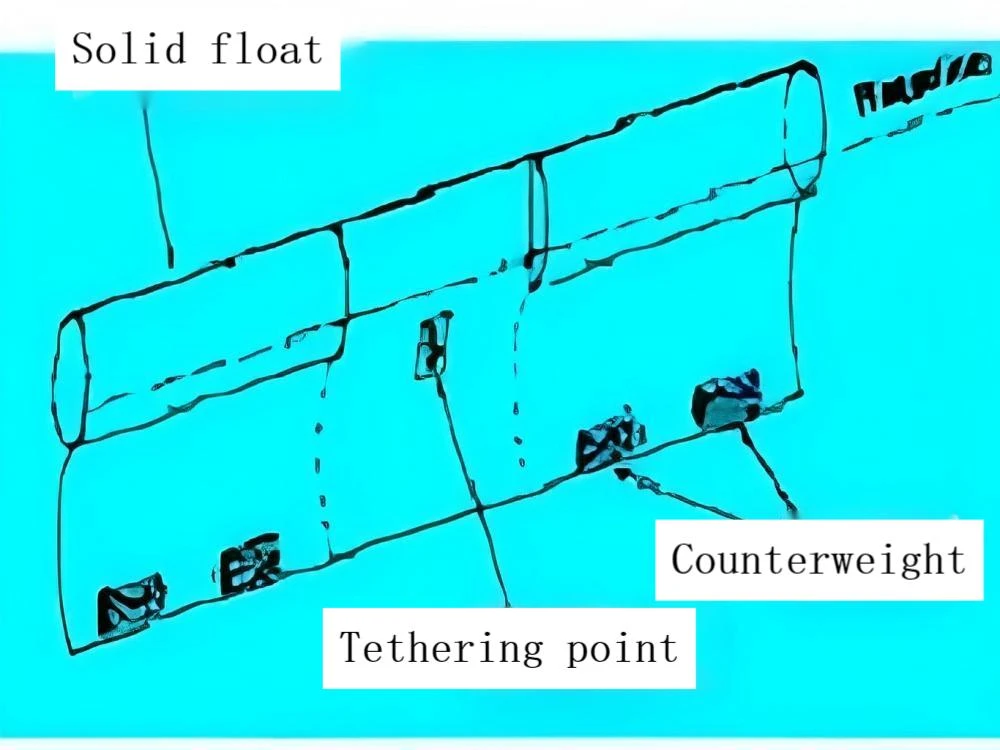
(3-7 Counterweights of Oil Booms)
(2) A curtain-type oil barrier filled with cylindrical or granular foam or made of steel materials is called a solid float-type oil barrier. Among them, the oil barrier with a floating body made of steel heat-resistant materials is also called a fireproof oil barrier.
The skirt of the curtain-type oil barrier is flexible and it can move relatively independently.
The tension band of the curtain type oil barrier is usually composed of steel chains or steel wire ropes, located at the lower edge of the skirt body. At the same time, this tension band also serves as a counterweight. The tension bands of some curtain-type oil booms are located beneath the floating body to replace the lower skirt body. Some curtain-type oil barriers use reinforcing belts instead of tension belts. For instance, the reinforcing belt in the middle of a PVC oil barrier serves as a tension belt.
The counterweight part of the curtain-type oil boom is attached below the skirt of the oil boom. The counterweight is usually steel chains or cast iron blocks (see Figure 3-7). In some oil booms, the counterweight is also found inside the skirt or directly suspended below the skirt.
In terms of structure, the curtain-type oil boom has the following characteristics: First, it has a high buoyancy-to-weight ratio, typically ranging from 5:1 to 20:1, and has good wave-following performance. The draft is three-fifths of the boom’s height, and the freeboard of the curtain-type oil boom is usually two-fifths of its height. Second, the inflatable curtain-type oil boom has a slow deployment speed, but it takes up less space when deflated and has a smooth surface that is easy to clean. The long-chamber inflatable curtain-type oil boom is easy and quick to inflate, but it is sensitive to punctures and cuts and has poor wave-following performance. Third, in terms of application locations, large inflatable curtain-type oil booms are suitable for open waters, while small ones are suitable for nearshore, ports and other sheltered waters with lower flow rates. Fourth, compared with inflatable oil booms, solid float-type oil booms have a fast deployment speed and are not sensitive to punctures, but they are complex to recover, require more work effort, and take up more space.
3.2 Fence-type Oil Boom
The fence-type oil boom (see Figure 3-8) is composed of floatation bodies, skirt bodies, tension belts and ballast weights, etc.
The floating body of the grid-type oil barrier is generally solid and arranged in the form of a grid. The skirt material is mostly made of glass fiber mesh or other rigid materials. The connection between the floating bodies adopts flexible partitions, making the floating movement of the oil barrier more flexible. The tension bands of the grid-type oil barrier are usually made of belts or steel wires and placed in the inner layer of the oil barrier. Counterweights are generally made of steel wire ropes, steel chains and cast iron blocks, etc.
According to the layout form of the floating body and the structural characteristics such as tension bands, people further classify the grid-type oil barrier into three types: central floating type, external floating type and external reinforcing band type.
1) The central floating type fence oil barrier has a group of central floating bodies, that is, the floating bodies are on both sides of the center line of the oil barrier and are symmetrical. The floating body group is usually composed of solid foam discs, and this buoyancy disc relatively reduces the storage volume of the oil barrier.
2) External floating fence oil barrier. The floating body of this type of oil barrier is generally set on one side of the oil barrier, and it can also be set on both sides of the oil barrier.
3) Install an external reinforced belt fence to enclose the oil barrier. This kind of oil barrier also comes in two types. One is to configure the reinforcing band on the side facing the power flow direction (see Figure 3-9); Another approach is to configure the reinforcing belts on both sides and fix them to the top and bottom of the oil barrier with steel wire ropes.
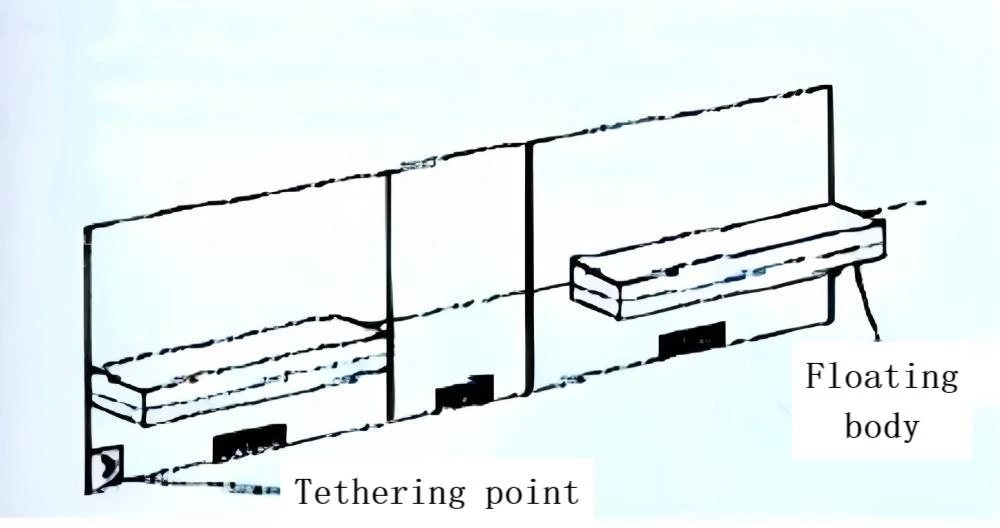
(3-9 External reinforced belt fence enclosing the oil barrier)
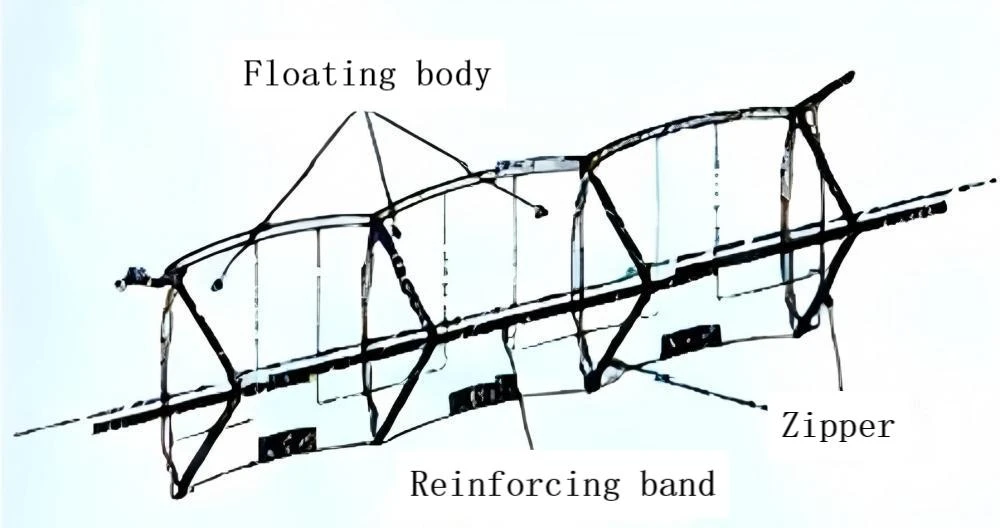
(3-8 Fence-type oil enclosure structure)
The characteristics of the fence-type oil enclosure are: low buoyancy ratio, generally ranging from 3:1 to 6:1, poor wave-following performance, and generally not suitable for open sea areas. The free board of the oil barrier accounts for one-third of the total height of the oil barrier, and the draft accounts for two-thirds of the total height.
It has good anti-tidal performance and is suitable for long-term deployment in relatively closed water areas and rivers. The central floating type fence has a small contact area with water, poor swinging performance and is prone to rolling. The external floating type fence oil barrier has a large contact area with water, which enhances the anti-rolling performance, but the strength of the external floating body in water is relatively weak. The external reinforced belt type oil barrier has good anti-tidal performance, but its layout is complex and the reinforcing belt is prone to entanglement during recycling. The single-sided reinforced grid-type oil barrier can only be used in unidirectional tidal current waters. Overall, this kind of oil barrier is easy to manufacture and has a relatively low cost, but it has a large storage volume. The covering materials for the oil barrier mainly include rubber, PVC and polyurethane, etc.
From the current actual usage perspective, the curtain-type and fence-type oil barriers are the most commonly used types of oil barriers. Some manufacturers of oil barriers, based on the respective characteristics of the curtain-type and fence-type oil barriers, produce oil barriers that fall between the two. Therefore, it is sometimes very difficult to strictly distinguish between the curtain-type and fence-type oil barriers.
3.3 Shore-type oil booms
When the oil spill spreads to the beach, it is difficult for ordinary oil booms to enclose the oil spill. Because when the water depth is less than the draft of the oil barrier, the oil barrier is very likely to tip over. In areas with high and low tides, the oil barriers are also difficult to adhere to the ground. At this point, the shore-type oil barrier should be used, and its structure is shown in Figure 3-10.
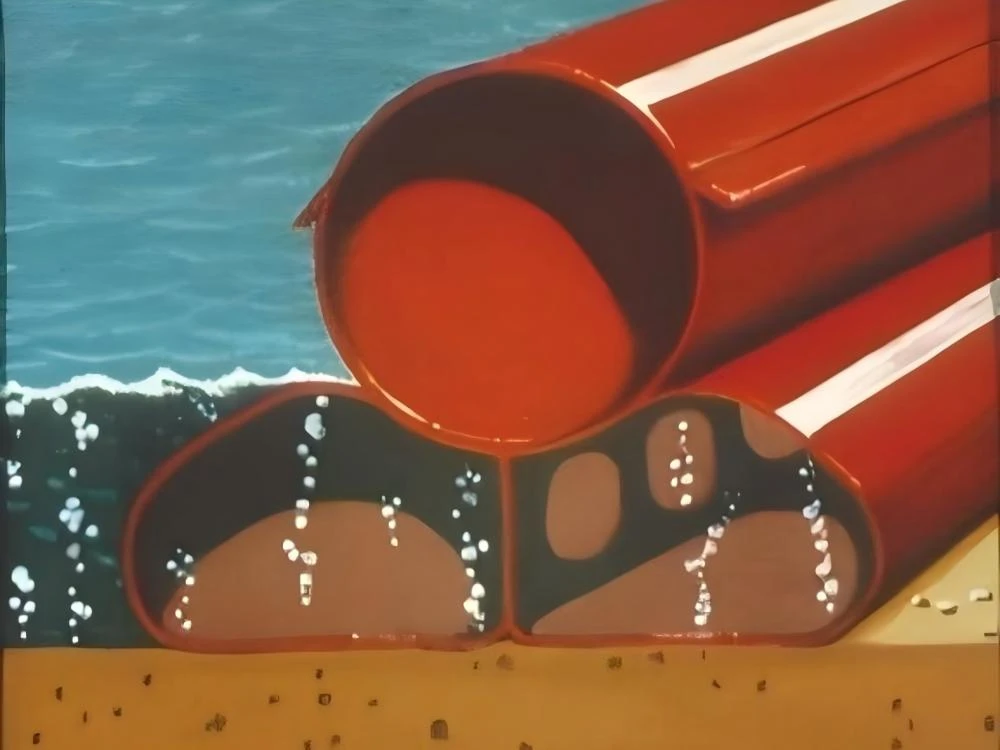
(3-10 Beach type oil enclosure structure)
The beach oil barrier is generally composed of three independent pipe cavities, each 10 to 25 meters long, forming a single unit. One of the pipe cavities is located at the top, while the other two are at the bottom, thus creating a “pin” shaped structure. The upper pipe cavity is filled with air and the two lower pipe cavities are filled with water to provide sufficient weight to keep the oil barrier in a sealed state with the ground or the beach.
The top tube cavity filled with air is the floating body of this kind of oil barrier, while the two tube cavities filled with water below are the skirt bodies of this kind of oil barrier. The draft is the vertical height of the two bottom pipe cavities after they are filled with water. The tension band is the structural material of the oil barrier itself. The counterweight is the water filled in the two bottom pipe cavities. At present, shore-type oil booms are mostly made of polyurethane materials.
As mentioned above, the shoreline type oil barrier is rather unique in design. The stemboard of this type of oil barrier is the height of a gas-filled tube cavity, and the draft accounts for approximately half of the total height of the oil barrier. The buoyancy ratio is usually 5:1 to 10:1. This type of oil barrier is very suitable for placement in the intertidal zone or at the junction of land and water to intercept oil spills. When using this type of oil barrier, generally, the placement location is selected first. Then, water and air are injected into the bottom pipe cavity and the top pipe cavity respectively. The amount of water injected should be appropriate; excessive water will affect the sealing effect with the ground.
From the structure of the shore-type oil barrier, the following main features can be summarized: Its application range is relatively narrow, generally only suitable for intercepting oil spills in the intertidal zone and at the junction of water and land. The ground where the oil barrier is placed should be relatively flat to achieve a relatively ideal sealing effect. On beaches with many rocks, the sealing effect will be affected. It can be connected and used in conjunction with other types of oil booms. Due to its unique structure, special care must be taken during deployment and recycling to prevent the surface from being punctured or scratched.
4. Oil barrier connector
The containment cage connector is a device used to connect each section of the containment cage to each other or to connect the containment cage to the quay wall, hull, etc. One function of the connector is to adjust the length of the oil barrier, and the other is to prevent the leakage of the floating oil between the oil barrier and the connected object. Different types and functions of oil barriers require different connectors for the oil barriers. When choosing a gas barrier, in addition to considering the various factors mentioned earlier, it is also necessary to focus on the connectors of the gas barrier itself, whether they meet the unified standards, and whether they can be connected and used with other gas barriers. This section introduces several common connectors.
4.1 Connectors between the oil booms
For ease of use, the oil barrier is usually equipped with a connector at certain intervals as needed, which is convenient for disassembly or connection. Considering factors such as the type and application area of the oil barrier, the connectors of the oil barrier vary greatly in terms of firmness and ease of disassembly, and there are many types. At present, there is no unified standard internationally. The United States requires the use of ASTM hook-type quick connectors, while China demands the use of three types of oil barrier connectors: hook-type, hinged type and rope-piercing type.
1) Hook type joint (see Figure 3-11) : Hook type joints have the advantages of convenient operation, easy connection and easy disassembly.
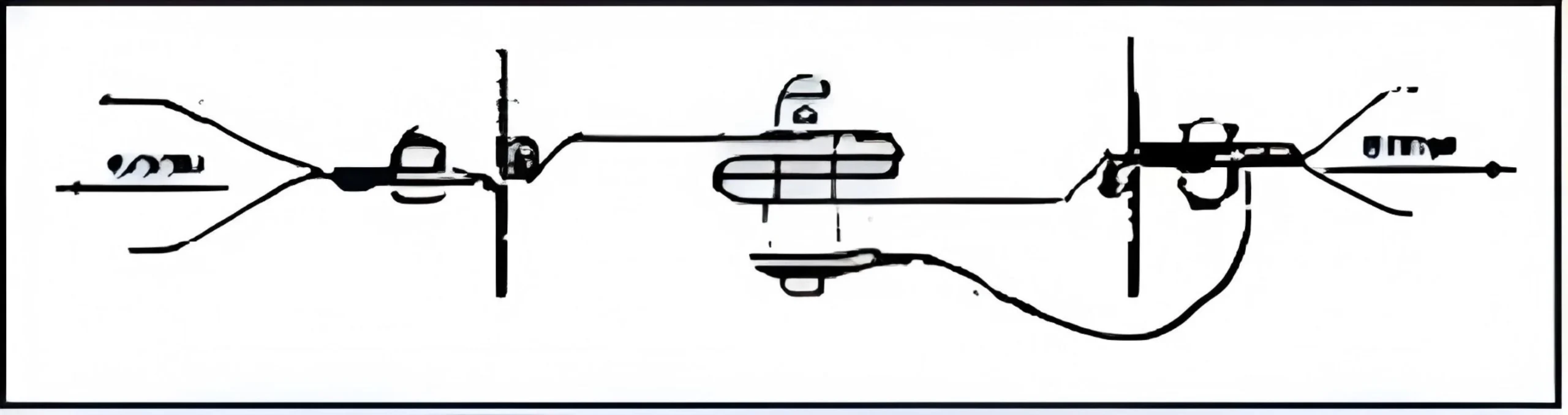
(3-11 Hook type joint structure)
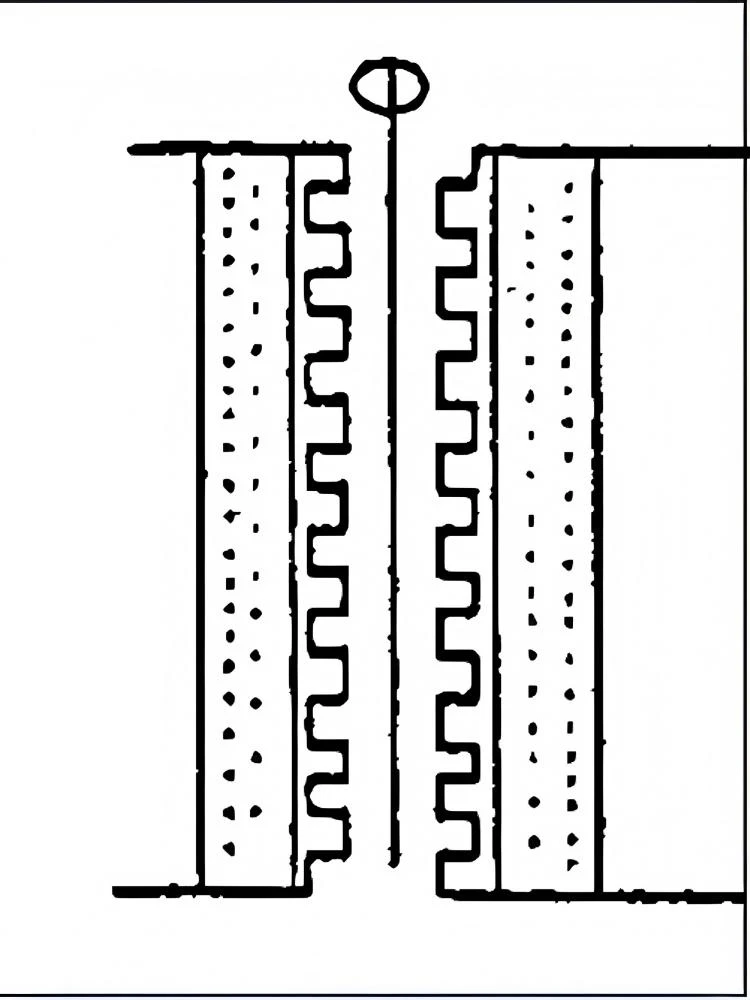
(3-12 Hinge type joint)
2) Hinge-type joint (see Figure 3-12) : Hinge-type joints have high strength and reliable connection, making them more suitable for long-term installation of oil barriers.
3) Rope-piercing joint: The rope-piercing joint is a relatively primitive and outdated type of joint, often used in PVC solid float oil booms.
4.2 Connectors between the oil barrier and the quay wall
After setting up oil barriers at ports and docks, in order to prevent oil from overflowing and running away, it is necessary to ensure the relative sealing between the oil barriers and the mating sections or objects such as the hull. Due to the rise and fall of the tide and the inability of people to adjust the height of the oil barrier in time, oil spills often occur within the enclosure, resulting in the oil barrier being rendered ineffective. For this reason, through continuous practice, people have developed a kind of connector called tidal compensator (see Figure 3-13). It can automatically adjust the height of the oil barrier in a timely manner as the tide rises and falls without human intervention. It is a vertical sliding device. Its structure mainly consists of a cylindrical floating body, a vertical sliding groove and a hoop sleeve. When necessary, the entire device only needs to be fixed to the corresponding shore wall and connected to one end of the oil enclosure. This sliding connector is not only not affected by tidal fluctuations but also ensures the sealing between the oil barrier and the quay wall.
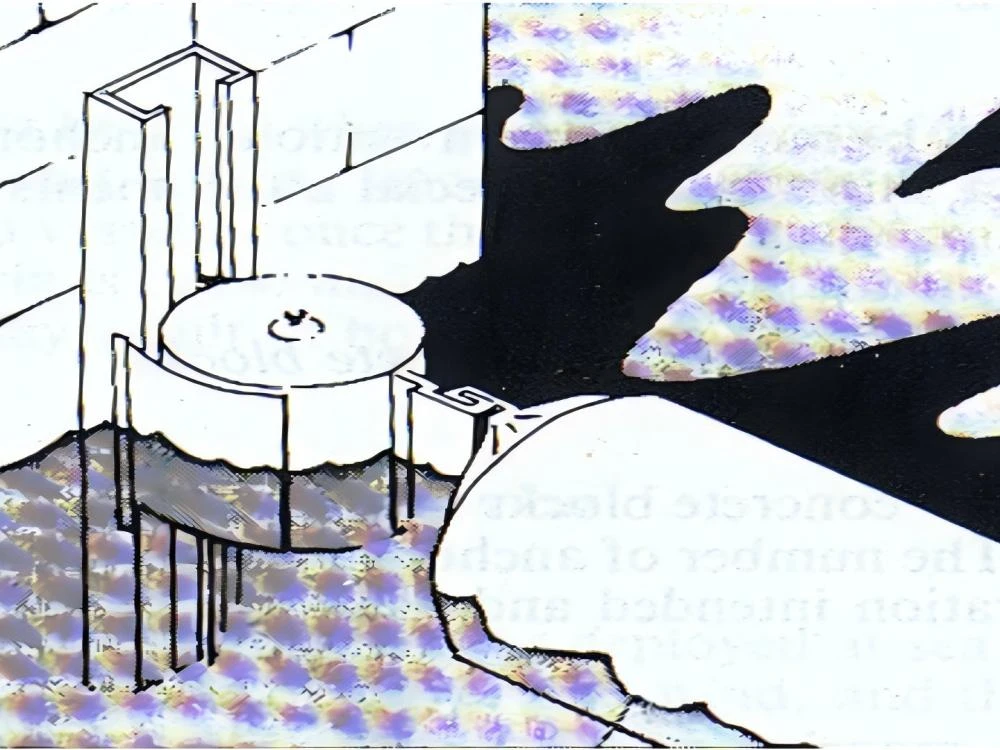
(3-13 Tidal Compensation Connector Structure)
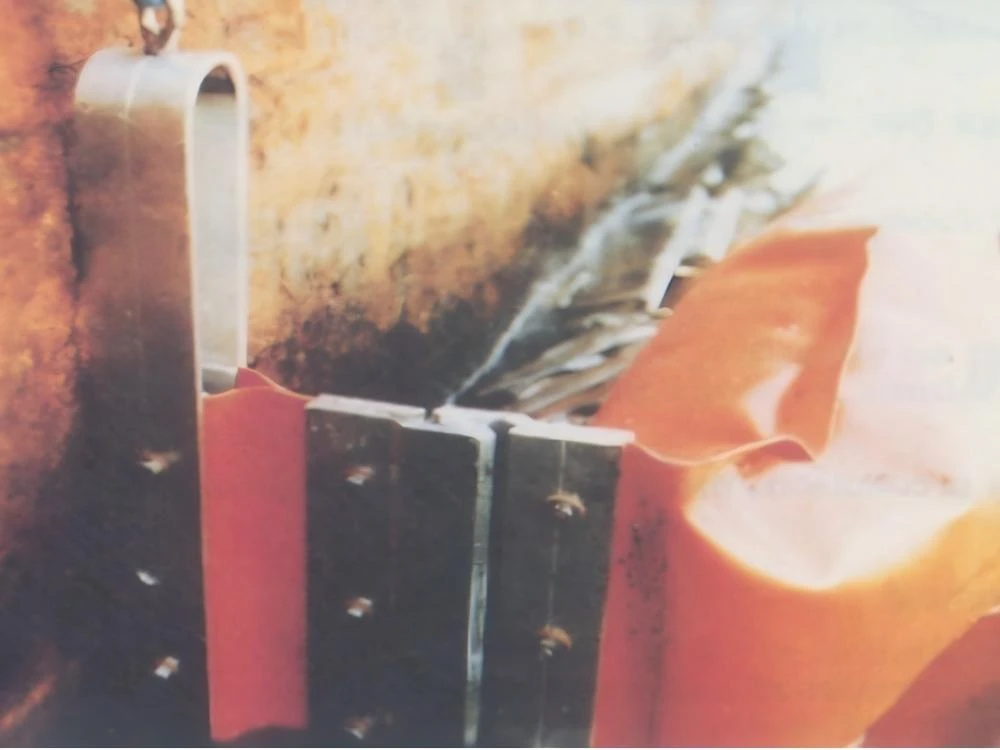
(3-14 Magnetic connector)
4.3 Connectors between the oil barrier and the hull
This type of connector is a magnetic connector. The highly magnetic magnet is attached to the hull. The operator can manually adjust the actual height of the oil barrier according to the ship’s draft or tidal conditions to achieve the purpose of controlling oil overflow.
From this, it can be seen that in order to prevent oil spill and leakage, when using this type of connector, it is necessary to arrange for on-duty personnel to supervise regularly and adjust the height of the connector at any time according to the tide and the draft of the ship, etc.
Section 2: Application of the Oil Barrier
1. Performance Requirements of the Environment for Oil Barriers
In the “Standards for Oil-Containment Booms”, the waters where oil containment booms are used are classified into four types of water conditions: calm waters, calm and rapid-flowing waters, sheltered waters, and open waters. Calm waters refer to the waters where the wave height is between 0 and 0.3 meters and the water current speed is below 0.4 meters per second; calm and rapid-flowing waters refer to the waters where the wave height is between 0 and 0.3 meters and the water current speed is 0.4 meters per second or above; sheltered waters refer to the waters where the wave height is between 0 and 1 meter; open waters refer to the waters where the wave height is between 0 and 2 meters or 2 meters or above. Different water environments have different requirements for the performance of oil containment booms. No oil containment boom can be applicable to all kinds of water environments. Only by choosing an oil containment boom that meets the performance indicators according to the specific water environment can the functions and effects of the oil containment boom be fully exerted. Table 3-1 introduces the performance requirements of oil containment booms for different water environments in the IMO demonstration tutorial.
Form 3-1 Performance Requirements for Oil Barriers in Different water areas
|
A calm lake bay with a wave height of less than 0.3 meters |
The water surface of a river with a current |
Nearshore waters of sheltered waters with a wave height of less than 1.5 meters |
Open waters with a wave height greater than 1.0 meter |
Freeboard |
0.2-0.5m |
0.3-0.5m |
0.4-0.6m |
0.5-1.0m |
Draught |
0.2-0.5m |
0.3-0.7m |
0.4-0.8m |
0.6-1.5m |
Buoyancy to weight ratio |
3:1-10:1 |
3:1-10:1 |
5:1-12:1 |
8:1-15:1 |
Total tension strength |
≥10Kn |
≥30Kn |
≥50Kn |
≥150Kn |
2. General Principles for Selecting Oil Booms
When selecting oil booms, the performance requirements of the water environment for the oil booms and the basic performance parameters of the oil booms should be considered first, and then the on-site environment and the operational performance of the oil booms.
2.1 Water environment: The water environment generally refers to three situations; the first is a calm water surface with a wave height of 0.3m (such as lakes and ports, etc.); the second is a calm water surface with current (such as rivers); the third is sheltered waters with waves higher than 1.0m and open waters with waves higher than 1.0m.
2.2 Performance parameters of the oil containment boom: Here, the performance parameters of the oil containment boom refer to the freeboard, draft, draft-to-weight ratio and total tension strength.
2.3 Operational performance of the oil containment boom: The operational performance of the oil containment boom usually includes the durability of the oil containment boom, easy deployment, good buoyancy, fast deployment speed, good shoreline sealing performance, easy maintenance and upkeep, convenient storage and applicability.
When choosing an oil containment boom, in addition to carefully considering all the aforementioned factors, one should also make a comparison in terms of performance and price based on the purpose of deployment, whether it is for containment, diversion, protection, or other factors such as deployment requirements, operating environment, and maintenance and usage. Thus, the most suitable oil containment boom for the actual situation can be selected. Table 3-2 lists the selection guidelines for oil containment booms in the “Oil Spill Emergency Plan for the Northern Sea Area”.
3.Examples of Selection of Oil-Fighting Booms:
3.1 Selection of Oil-Flooding Barriers in Open Water Areas
When choosing an oil containment boom in open waters, the following factors should be mainly considered: (1) The strength of the boom: The selected oil containment boom must be strong enough to withstand various external forces brought by wind, waves and tides to the boom; (2) Ease of deployment: The selected oil containment boom should be able to be conveniently deployed from the ship or other places onto the water surface and form an ideal containment shape; (3) Storage space: When an oil spill occurs, the ships heading to the spill site may carry a large number of emergency equipment. At this time, it is necessary to consider whether the ship’s deck has sufficient space; (4) Buoyancy-to-weight ratio: Experience shows that the buoyancy-to-weight ratio of the oil containment boom deployed in open waters should be above 8:1; (5) Freeboard and draft: The dimensions of freeboard and draft should be determined by the wave height and tidal conditions of the water area where the vessel is operating.
Taking into account all the various factors mentioned above and referring to Table 3-2 of the Guidelines for the Selection of Oil-Containment Boats, it is not difficult to see that for open waters, inflatable curtain-type oil containment booms are the most ideal choice.
3.2 Selection of Oil-Fighting Booms for Rivers and Nearshore Waters
When deploying oil booms in rivers and nearshore waters, the general purpose is to divert oil spills. The deployment areas are relatively wide and the deployment time is relatively long. Therefore, when choosing oil booms, the main factors to be considered are: (1) Resistance to puncturing: It is recommended to use solid float-type oil booms or inflatable rubber oil booms that are less sensitive to puncturing; (2) Flow and tides: In areas with weak currents, standard center-type grid-type oil booms can be used; in rapids and strong water flow areas, grid-type oil booms with reinforced belts or curtain-type oil booms with weighted chains as reinforcement belts can be selected.
3.3 Selection of Oil-Fighting Booms in the Water Area Surrounding the Wharf
For the purpose of protecting the waters of the wharf, the first consideration should be the ease of rapid deployment. Self-inflating oil booms or solid foam barrier oil booms are suitable for this purpose. If the water flow at the wharf area is rapid, barrier oil booms or solid floatation type oil booms should be selected. If fixed or semi-fixed oil booms are deployed at a berth with strong waves, oil booms with high strength and high floatation-to-weight ratio should be chosen. Rubber oil booms or solid foam barrier oil booms are suitable for this situation. These two types of oil booms are less sensitive to sharp objects.
Form 3-2 Guidelines for Selecting Oil-Fighting Booms
Symbol Description 1、Good 2、Middle 3、Poor |
Type of oil containment boom |
|||||
Solid float type |
Inflatable type |
Self-inflating type |
Tension member type |
Fence type |
||
Environmental Conditions |
Offshore Hs>3ft V<1kn |
2 |
1 |
2 |
1 |
2 |
Port Hs>3ft V<1kn |
1 |
1 |
1 |
2 |
2 |
|
Calm water Hs>3ft V<.5kn |
1 |
1 |
1 |
2 |
1 |
|
High velocity flow V>1kn |
2 |
2 |
3 |
1 |
3 |
|
Shallow water Depth of water<1ft |
1 |
2 |
2 |
3 |
3 |
|
Performance Characteristic |
For use in the presence of rough objects |
1 |
2 |
3 |
3 |
2 |
Excess buoyancy |
2 |
1 |
1 |
2 |
3 |
|
Stochastic Volatility |
2 |
1 |
1 |
2 |
3 |
|
Strength |
2 |
1 |
3 |
1 |
1 |
|
Operating Characteristics |
Movable |
2 |
2 |
1 |
3 |
2 |
Easy to clean |
1 |
1 |
1 |
3 |
1 |
|
Squeezability |
3 |
1 |
1 |
2 |
3 |
4. Deployment Forms of Oil Containment Boats
The containment, diversion and prevention functions of oil containment booms for oil spills can be achieved through appropriate deployment forms. According to different types of water areas, the deployment forms of oil containment booms can mainly be divided into two situations: the deployment forms in open waters and those in nearshore areas and rivers.
4.1 Deployment forms of oil booms in open waters
When deploying oil booms in open waters, the form mainly depends on the purpose of deployment and the number of vessels involved in the deployment operation. Typical deployment forms include single-vessel deployment (single-side towing and double-side towing), two-vessel deployment, and three-vessel deployment.
(1) Single-ship deployment form
The single-ship deployment form requires equipment such as oil spill recovery vessels, extendable rods (extendable arms and buoys), oil containment booms or oil containment booms equipped with skimmers. The length of the extendable rods is selected according to the size of the vessel, and it is generally 5-15 meters. Single-ship towing can be carried out with single-side towing (extending the extendable rods from one side of the vessel) for surface oil spill containment and sweeping, or double-side towing (extending the extendable rods from both sides of the vessel). The shape of the single-ship towing the oil containment boom is usually V-shaped, as shown in Figure 3-15. However, when deploying large-scale oil containment booms in this form, the maneuverability of the vessel will be limited to a certain extent.
Single-sided V-shaped towing involves connecting the oil containment boom to the vessel and the top of the extended arm respectively. The length of the V-shaped boom on one side is usually from 10m to 50m, mainly depending on the size of the vessel. This deployment form can only form one recovery area, so the skimmer should be placed at the bottom of the V-shaped boom, that is, the place where the oil spill is most concentrated, for recovery. During the recovery process, it is necessary to observe and adjust the boom arm continuously to make the bottom of the V-shaped boom as close to the ship’s side as possible for easier recovery. If the recovered oil spill is in a solid state during single-sided towing, a collection net should be used for recovery.
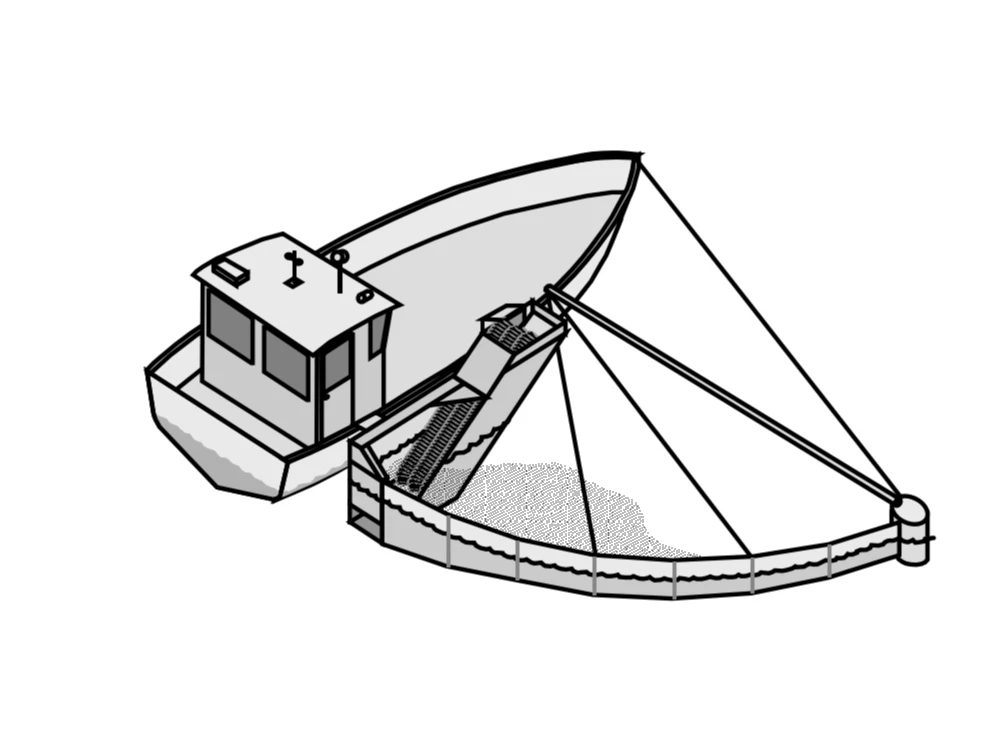
(3-15 Single vessel single-side towing of oil booms)
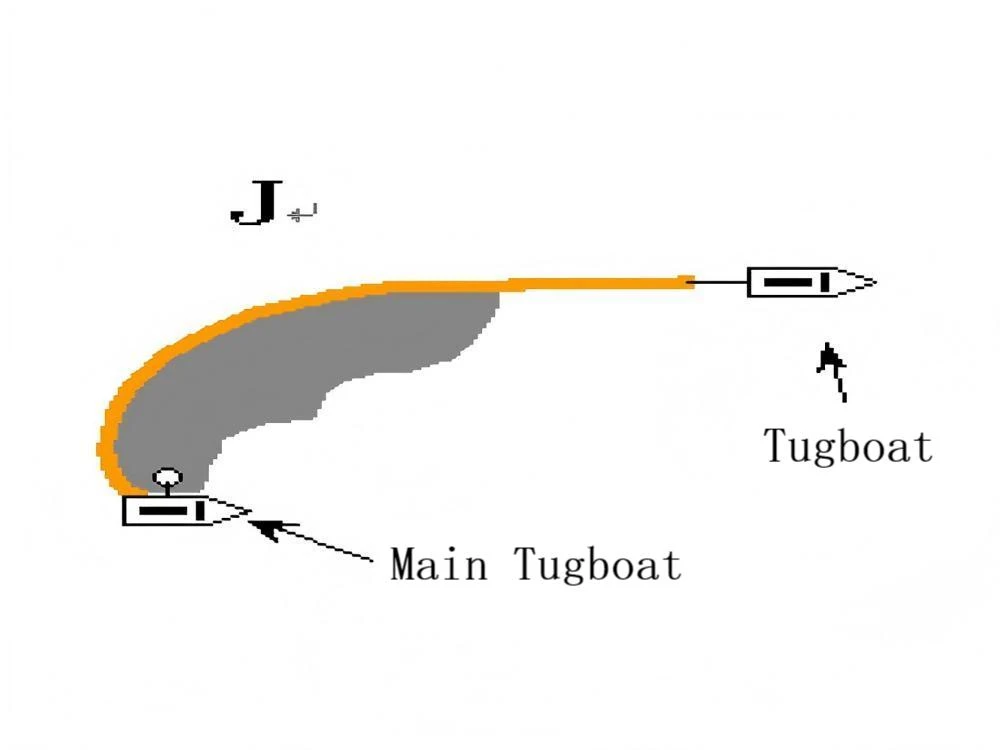
(3-16 Two vessels deploying an oil-boom in a J-shaped pattern)
If oil booms are deployed on both sides of a vessel, two recovery areas can be formed. This not only ensures that the forces on both sides of the vessel are basically the same, but also makes the vessel easier to maneuver in this situation compared to when it is deploying booms on only one side. It is worth noting that deploying booms on both sides requires a spacious area. If the water area that can be towed is narrow, double-sided towing cannot be adopted.
A successful double-sided towing operation requires a large number of related equipment. Therefore, for a vessel, it demands a wide deck space to store sufficient oil spill recovery and storage equipment as well as enough space to accommodate emergency personnel for clean-up operations.
(2) Deployment forms of the two vessels
For deploying the oil containment boom by two vessels, the J-shaped deployment is usually adopted, also known as J-shaped towing (see Figure 3-16).
This deployment form generally requires two vessels. One serves as the main towing vessel, used to tow the shorter end of the oil containment boom and store the necessary recovery equipment and recovery personnel; the other serves as the towing vessel, used to tow the longer end of the oil containment boom. The length of the oil containment boom should be 200-400m. The length of the oil containment boom from the main towing vessel to the bottom of the J-shaped structure is 20-40m, and the skimming device is placed at the bottom of the J-shaped structure. The oil containment boom should be as close as possible to one side of the main towing vessel (10-20m) to facilitate the operation of the skimming device or other recovery equipment.
In order to obtain and maintain the ideal shape of the bottom of the oil containment boom, the shape of the bottom of the boom can be appropriately adjusted by pulling the rope connecting the boom with the ship.
When the two-ship deployment form is used for the oil spill diversion purpose, the length of the oil containment boom is generally 100 – 400 meters. If the boom is too long, it will be difficult for the auxiliary vessel to maintain the ideal position, and the efficiency of the system will decline.
When conducting the operation of towing two vessels, generally speaking, the main towing vessel serves as the commanding vessel. The main towing vessel should promptly and accurately issue instructions to the preceding towing vessel based on the situation of oil spill containment and sweeping. The towing vessels should maintain good communication with the main towing vessel at all times and adjust their course and speed in accordance with the instructions in a timely manner. Only in this way can a good J-shaped containment and sweeping form be maintained at all times, achieving the desired effect of oil recovery.
(3) Deployment Form of Three Vessels
In order to increase the coverage area of oil spill containment, people gradually discovered in practice that using three vessels for deploying and sweeping oil containment booms is more effective. The deployment form of three vessels usually adopts U-shaped (see Figure 3-17) or open U-shaped containment shapes. The U-shaped containment mainly uses two vessels to tow the oil containment boom in parallel. During towing, the length of the oil containment boom generally needs to be 600 meters. Compared with J-shaped towing, towing in parallel with two vessels is easier to maintain the correct position. While the first two towing vessels are advancing simultaneously, the third vessel should always be on the outside of the bottom of the U shape, based on the speed of the two towing vessels, and use other suitable recovery equipment such as skimmers to recover the spilled oil trapped at the bottom of the U shape. This form of containment and sweeping operation has a large recovery volume. Therefore, before the operation, it is necessary to fully consider the capacity of the third vessel (the recovery vessel) to avoid having to return halfway or repeatedly change the recovery vessels due to insufficient capacity, which brings inconvenience to continuous operation.
The open U-shaped containment structure is developed from the U-shaped containment structure. The two sections of oil containment booms extend 3-10m to both sides at the opening, forming a funnel. The bottom of the U-shaped structure is adjusted by ropes to make the opening width 5-10m, thereby reducing the impact of turbulence on the floating oil. This form can control the flow of spilled oil and make the recovery work easier. Then, through the third vessel, spill oil recovery is carried out using single-side or double-side containment sweeping.
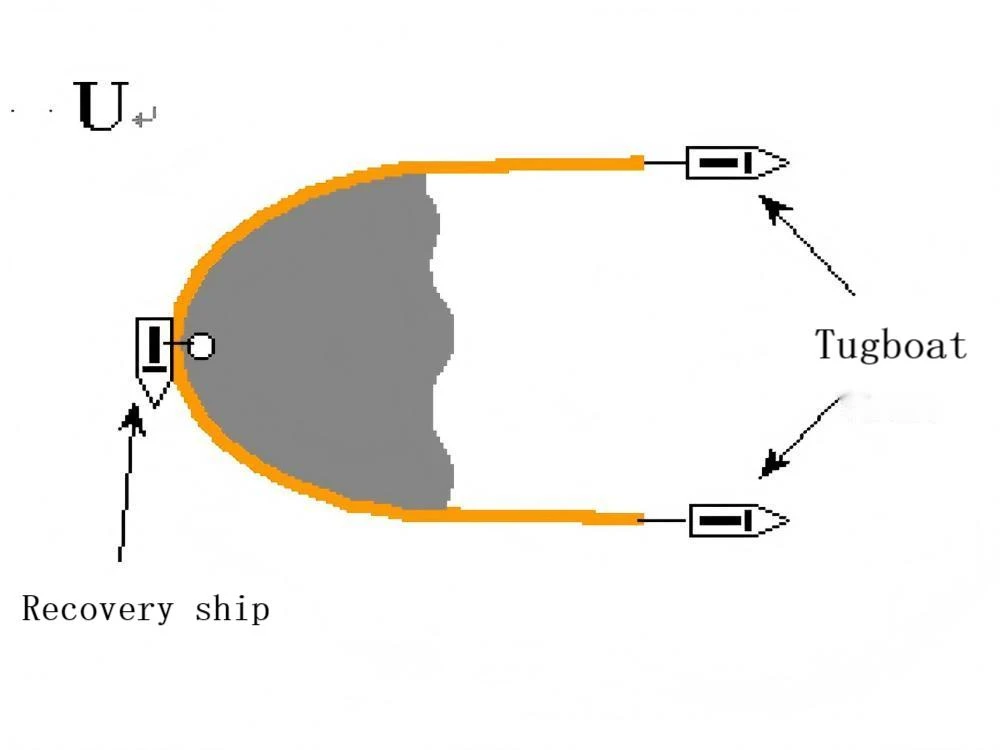
(3-17 Three-ship U-shaped deployment of oil booms)
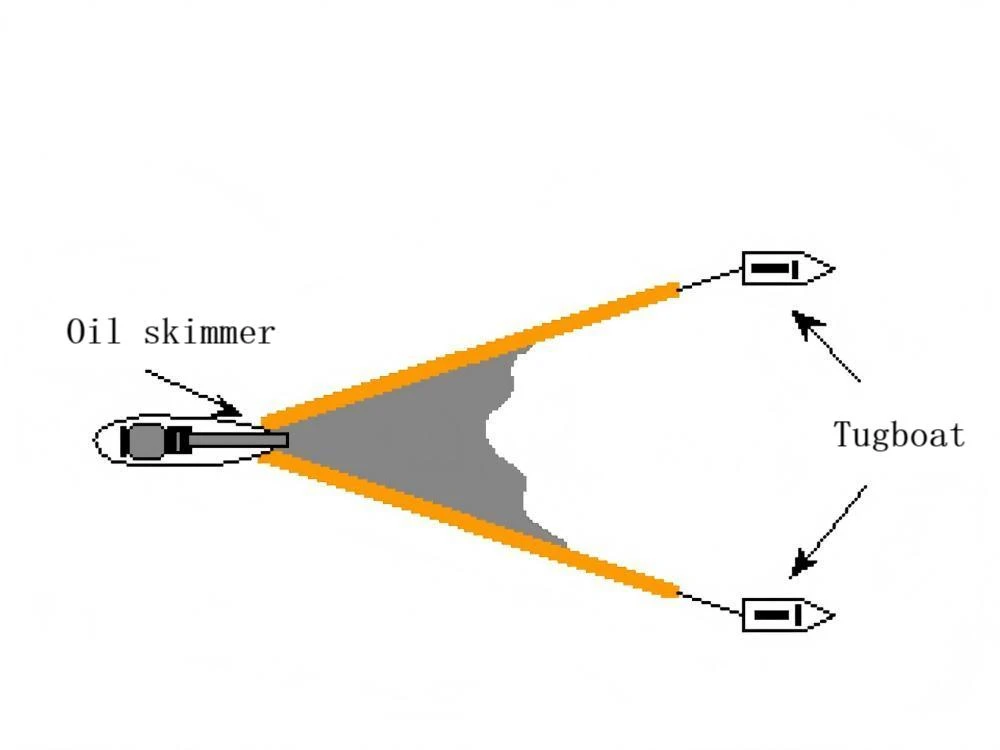
(3-18 Three vessels deploy the oil containment boom in an U-shaped pattern)
The three deployment forms mentioned above, no matter which one it is, as the main towing vessel or the vessel responsible for the recovery operation, when conducting the enclosed sweeping recovery operation, one should always pay attention to observing whether there are vortices or re-appearing oil films floating behind the oil containment boom. If such phenomena occur, it indicates that the towing speed is too fast. The vessel should gradually slow down until these phenomena disappear.
4.2 Deployment forms of oil booms in nearshore waters and rivers
For the deployment of oil booms in nearshore waters, the form adopted often depends on the purpose of deployment. If the purpose is to contain oil spills, especially in areas such as intertidal zones where land and water alternate, it is best to use the form where the shore-based oil boom is connected with other booms and used in series, placing the end connected with the shore-based boom on the side closer to the shore. If it is for diversion, it should be deployed in a multi-layer overlapping form for stepwise diversion. In rivers, for the purposes of oil spill containment or diversion, the main deployment forms of oil booms include shoulder-mounted and staggered shoulder-mounted forms (see Figure 3-19).
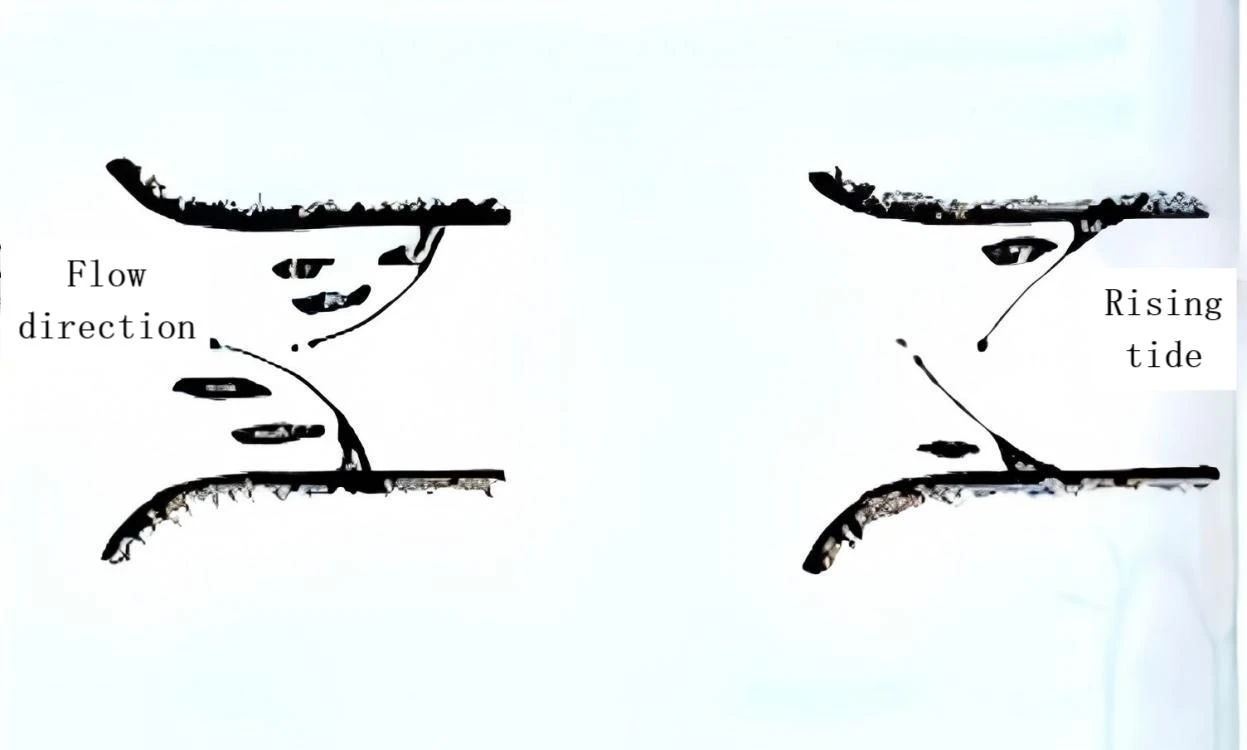
(3-19 Shoulder badge style and interlaced shoulder badge style deployment forms)
The deployment methods of oil booms in nearshore areas and rivers are different from those in open waters. To ensure the effectiveness of the booms, the following factors should be mainly considered:
(1)Water Environment: The water environment referred to here mainly refers to the flow direction and velocity of the proposed protected water area, so as to determine the reasonable deployment angle. Experience shows that when the flow velocity relative to the vertical direction of the oil containment boom exceeds 0.7 knots, the spilled oil is likely to escape from under the oil containment boom and cannot achieve the purpose of oil containment. Therefore, when deploying the oil containment boom in rivers or coastal waters, attention should be paid to forming a certain angle between the deployment of the oil containment boom and the flow direction, and adjusting it in time according to the change of the flow direction to alleviate the drift speed of the spilled oil relative to the oil containment boom. The larger the flow velocity, the smaller the angle between the oil containment boom and the flow velocity should be. At the same time, attention should also be paid to the length of the oil containment boom. Depending on specific needs, the length of the oil containment boom should be increased or decreased. Generally, in the river area, for oil spill containment, the length of the oil containment boom is approximately twice the width of the river. Due to the rapid flow of the river, the phenomenon of spilled oil escape often occurs. In response to this situation, multiple oil containment booms can be overlappedly deployed to reduce the occurrence of spilled oil escape. Table 3-3 lists the deployment angles and lengths of the oil containment booms in rivers.
Form 3-3 The required angle and length for deploying oil containment booms in the river.
Flow rate (knot) |
The angle (in degrees) between the oil containment boom and the shoreline |
The length of the oil boom relative to the width of the river |
0.7 |
90 |
1.0 times the width of the river |
1.0 |
45 |
1.4 times the width of the river |
1.5 |
30 |
2.0 times the width of the river |
2.0 |
20 |
3.0 times the width of the river |
2.5 |
16 |
3.5 times the width of the river |
3.0 |
15 |
4.3 times the width of the river |
3.5 |
11 |
5.0 times the width of the river |
4.0 |
10 |
5.7 times the width of the river |
5.0 |
8 |
7.0 times the width of the river |
For example: The flow rate is 1.5 knots, the deployment angle is 30 degrees, and the length of the oil containment boom should be twice the width of the river.
(2) Selection of the locations for deploying oil booms. Most rivers have relatively calm water areas, which are generally located on the inner side of river bends, in areas with vegetation, or where rocks protrude. These are the best locations for oil spill diversion and also ideal places for oil spill recovery (see Figure 3-20).
When implementing the containment operation, based on the navigation conditions, the oil containment boom can be divided into two parts for oil spill interception. Do not place the oil containment boom across the river to avoid hindering the entry and exit of vessels to and from the area. Moreover, in terms of the deployment form of the oil containment boom, under certain conditions, shorter oil containment booms are easier to be deployed and formed than longer ones. This point should be taken into consideration during the deployment operation. As long as the containment objective can be achieved, the length of the oil containment boom should be shortened as much as possible. This can also reduce the subsequent work of oil containment boom recovery and cleaning.
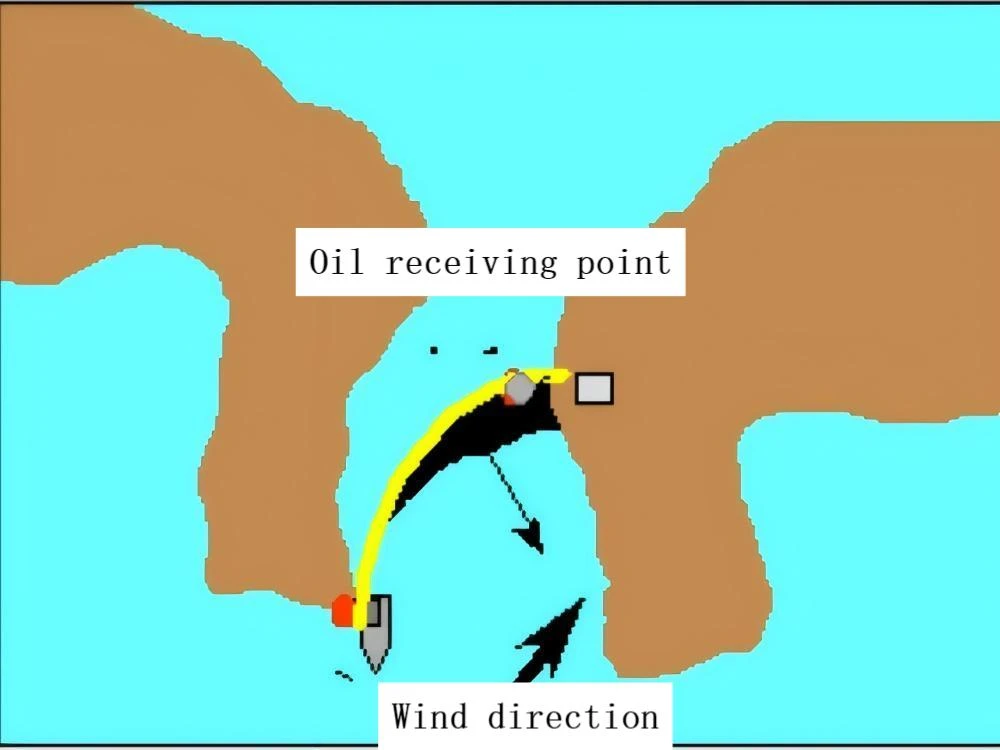
(3-20 Selection of Deployment Locations for Oil Spill Control)
During the operation of oil spill containment, it is often observed that while the oil containment boom is controlling the oil spill, a considerable amount of garbage, such as weeds, branches and leaves, will mix with the floating oil and float in together, gathering on the side of the containment boom. Generally, these garbage will not cause any damage to the containment boom, but they will have some impact on the skimmers used in the recovery operation. Therefore, the operation personnel should pay attention to observing and, as soon as possible, remove the garbage to ensure that the skimmers can continuously and efficiently carry out the oil spill recovery operation.
In order to prevent floating garbage from entering the oil booms, logs can be placed upstream of the booms to intercept the garbage in advance, thereby reducing the impact of floating garbage on the booms on the water surface. The logs used for intercepting garbage must be securely fastened to avoid being washed away by the water flow and causing unnecessary damage.
(3) Tidal range and water depth of the local waters: In the nearshore and shallow water areas, when deploying oil booms, it is necessary to consider whether the tidal range and water depth of the area can meet the draft requirements of the oil booms. Generally speaking, the water depth in the area where the oil booms are deployed should be at least three times the draft of the oil booms. Otherwise, if the water depth is insufficient, even if the oil booms are deployed, they will lose their containment effect. For shallow water areas or areas with insufficient water depth, it is best to consider using them in combination with shore-based oil booms according to the actual situation to prevent accidental oil spill from causing pollution to the riverbanks and intertidal zones.
5. Deployment of Oil-Fighting Booms
Before deploying the oil-fighting booms, they should be assembled as completely as possible on the land or on the deck of the vessel according to the required approximate length. The required length can be referred to in Table 3-4 for the deployment length of oil-fighting booms under normal conditions. There are many methods for deploying oil-fighting booms depending on the type of booms and the usage area. They can be deployed from the shore, the wharf, the vessel, from the reel, from the container, or from the platform. The common methods are deployment from the vessel and deployment from the shore.
Form 3-4 The deployment length of the oil containment boom under normal conditions
Application scenarios |
Water environment |
Length of the oil-boom |
Blockade of the sunken vessel |
Depends on the sea conditions |
3X the length of the ship |
Containment of leakage at the loading and unloading point |
Calm water area or depends on the sea conditions |
1.5X the length of the ship |
Used in conjunction with an oil skimmer |
On the sea |
460 – 610 meters of each skimming device |
Protect the river estuary |
Calm water area |
3-4 times the width of the water area |
Protected bays, harbors, marshes |
Calm water area or depends on the sea conditions |
(1.5 times+flow rate) of width of the water area |
5.1 Deploy from Ship
When deploying the oil booms from a ship, they should be stored and fixed on the ship’s deck. The following steps should be followed when deploying the oil booms from a ship:
(1) Selection of towing vessels. When deploying oil containment booms, choosing the right towing vessels is also crucial for achieving effective containment. When selecting towing vessels, one must consider the towing capacity of the vessels. Generally, it can be calculated that for every 200 (Newton) of towing force, it is equivalent to 1 horsepower of the engine inside the vessel. For example, if a single vessel towing is responsible for containing an oil spill boom with a resistance of 20,000 (Newton), a vessel with a towing capacity of more than 100 horsepower must be selected. If a U-shaped towing with a resistance of 40,000 (Newton) is carried out using two vessels, two vessels with a towing capacity of more than 1,000 horsepower each must be selected. In addition to considering the towing capacity, when the towing vessel is also responsible for oil spill recovery (single vessel deployment), the deck space must also be considered, whether it is sufficient to load the necessary cleaning and pollution control equipment, and whether there is sufficient cargo space.
(2) Determination of Deployment Scheme. The success of rapid deployment of oil containment booms and their effectiveness in controlling oil spills is highly dependent on the determination of the deployment scheme. Main considerations should include the type of containment booms to be used, their length, the deployment platform, and the deployment methods. Taking vessel deployment as an example, the scale of the oil spill and the surrounding water environment should be taken into account to determine the size of the main and auxiliary tugboats and their supporting auxiliary equipment. At the same time, the number of personnel involved in the containment operation on board the vessel should be determined, and their responsibilities should be clearly defined. Specific operation steps and communication methods should be clarified, and the towing route should be preliminarily drawn up to ensure that each participant is well-informed and that the actions are unified and in step. After the deployment scheme is determined, all vessels and personnel involved in the containment operation must strictly fulfill their duties and obey the unified command of the commanding personnel or the commanding vessel.
(3) Preparations before Deployment. Before officially deploying the oil containment boom into the water, it is necessary to check whether all matters related to the containment operation have been prepared in place. For example, if the oil containment boom is scattered on the deck, each unit of the oil containment boom should be connected well, and one end of the oil containment boom as well as other equipment that does not need to enter the water should be fixed on the deck of the vessel. If there are no reinforcement points on the deck of the deployment vessel, reinforcement equipment should be set up to prevent equipment that should not enter the water from being accidentally dragged into the water during the operation. The towing rope of the oil containment boom must be firmly connected to the deck of the vessel in advance. Personnel specifically responsible for the deployment operation should wear life jackets, take their positions, and pay attention to their own safety.
Generally speaking, if a grid-type oil containment boom and a solid float-type oil containment boom are used for deployment, the storage device of the oil containment boom can be placed at the stern of the vessel. This is because it does not require too much space and the deployment operation is more convenient. However, if an inflatable oil containment boom is used, the storage device of the oil containment boom and the stern of the vessel usually require a large deck space. The size of the deck space depends on the length of each air chamber of the oil containment boom, and it is usually 5-6 meters. In summary, the deck space should be sufficient to meet all the operation links for deploying the oil containment boom.
(4) Deployment operation. During the process of deploying the oil containment boom, the deployment vessel should move slowly. After the boom is released for 10 to 20 meters, the speed of the vessel should be increased according to the specific situation. The remaining boom can be pulled out by relying on the resistance force generated by the water on the boom. Generally, the straight towing speed of the oil containment boom is about 5 knots. For the strong-breaking oil containment boom, the straight towing speed can reach 7-8 knots, but not more than 10 knots. The curve towing speed is 3-4 knots, and the U-shaped towing speed is less than 2 knots. During the towing process, it is necessary to prevent the oil containment boom and the towing equipment from getting tangled in the propeller.
The above deployment method does not require an auxiliary vessel. Of course, using an auxiliary vessel can make the deployment operation easier and safer. However, the two vessels should maintain communication to avoid accidents.
Place the grid-type oil containment boom, the solid float-type oil containment boom or the self-inflating oil containment boom. Generally, no other operations are required and they can be deployed immediately. When multiple sections of the oil containment boom need to be stored on the deck, they can be placed on one side of the vessel to facilitate the connection between the sections. During deployment, start from the oil containment boom at the stern of the vessel and deploy the subsequent sections one by one in close succession.
Before deploying the inflatable oil containment boom, use an inflation machine to inflate it. At this time, the winch should rotate slowly. When the last few sections of the oil containment boom are deployed, operate with extra caution to avoid the other end of the boom also falling into the water.
The towing rope of the oil containment boom must be firmly connected to the vessel’s deck in advance. When deploying the last section of the oil containment boom, first deploy the freely floating towing rope, then tie the towing rope of the oil containment boom to a mooring post or similar object and secure it on the auxiliary tugboat. At this point, the formed oil containment boom can begin its containment operation.
5.2 Deployment from the shore
Deployment of oil booms from the shore should be carried out after choosing the appropriate location for deployment in advance. The oil booms can be dragged into the water from the shore by using vessels and manpower against the current to form the required shape.
The procedure for deploying oil booms from the shore is basically the same as that for deploying them from vessels. The difference is that an auxiliary vessel is needed. One person on the shore needs to give instructions and maintain communication with the vessel.
When one end of the oil containment boom is fixed on the shore, the auxiliary vessel should tow the boom and keep it in the correct position. In the nearshore area with very high current velocity (3-6 knots), deploying a 200-meter-long oil containment boom requires a powerful vessel to maintain the correct position of the boom. In the area with significant tidal variations at the wharf, the tidal range should also be considered.
In addition, although aircraft transportation for deploying the oil containment boom is fast, it is rather complicated and can only deploy self-inflating oil containment booms.
6. Anchoring of Oil Containment Booms
Among various deployment forms of oil containment booms, due to the influence of various factors such as wind and current, it is difficult for the booms to maintain the predetermined shape and achieve the purpose of containing oil spills. For instance, using ships to maintain the shape of the booms during deployment is very costly. In contrast, using anchors is more economical. Therefore, when dealing with relatively fixed oil spill sources, using anchors to maintain the containment shape of the booms is the most common practice. Before anchoring the booms, especially when they need to be left overnight after deployment, it is necessary to understand the local water conditions and meteorological information in advance. Anchoring the booms requires not only anchors but also release ropes, anchor chains, float buoys, drag heads, lights, and other accessories. For some waters that require special protection, corresponding types of cats can be pre-deployed to prevent unexpected situations.
6.1 Anchor using environment
When using an anchor, one should be familiar with the relevant conditions such as the bottom structure (sand, stones or rocks), flow direction, flow velocity and water depth to ensure the size of the anchor (see the table below) as well as its effectiveness and safety.
The use of anchors has two scenarios:
(1) If the flow direction of the water area where the oil booms are deployed is unidirectional, the anchor must be placed on the side of the oil booms facing the flow direction.
(2) If the flow direction changes, such as in the intertidal zone, anchors should be set on both sides of the oil booms. Most oil booms have anchor seats or oil boom joints that can be connected to anchors.
6.2 Number of Anchors Used
The number and size of anchors to be used depend on the forces (wind, current, waves) acting on the oil containment boom, the direction of flow, the length of the oil containment boom, the size of the vessel, and other factors. Generally, for a floating oil containment boom (with a height of about 1.2m), 40-80m requires one or two anchors to be deployed. For an inflatable oil containment boom (with a height of 2m), 2-4 anchors can be deployed for 100m.
According to the requirements of the “Standard for Oil Spill Containment Booms” regarding the anchors used for oil spill containment booms, when using manual deployment and retrieval anchors, the weight of each anchor should not exceed 150kg. The types of anchors can be large holding force anchors, fishing gear anchors, v-shaped anchors, naval anchors, Danforth anchors, four-pronged anchors, or single-arm anchors. Usually, anchors weighing 20-100kg with lifting devices are used.
6.3 Anchoring Force
When anchoring is necessary, the anchoring force is the key factor determining whether the oil containment boom can maintain an effective containment form to achieve oil containment. Generally, one should first understand the anchoring force of the anchor (refer to Table 3-5), and then make the correct choice based on the water area and soil conditions.
Form 3-5 The grip of the Danforth anchor
Anchor weight(kg) |
Holding power(kg) |
||
---|---|---|---|
|
Mud |
Sand |
Clay |
15 |
200 |
250 |
300 |
25 |
350 |
400 |
500 |
35 |
600 |
700 |
700 |
The anchoring force of the anchor is also affected by other factors, mainly depending on the angle between the anchor chain and the seabed. The most suitable angle is 0 degrees. If the anchor chain is lifted by more than 10%, the anchoring force of the anchor will significantly decrease. Connecting the anchor chain to the anchor chain can reduce the movement of the anchor chain. Similarly, using the anchor ball can prevent the anchor chain from being lifted. The anchor ball can form a certain angle between the oil containment boom and the anchor rope. This angle can reduce the impact of the movement of the oil containment boom system on the anchor system. As shown in Figure 3-21.
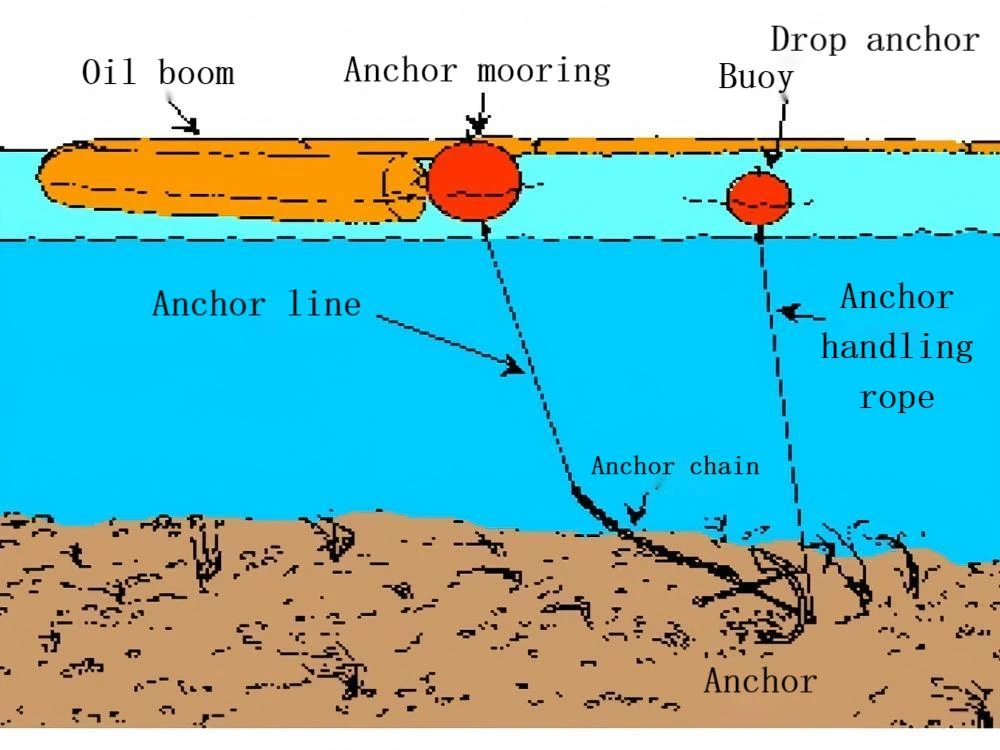
(3-21 Deployment forms of anchors used)
To prevent the anchor from being lifted by wave action, the length of the rope connecting the anchor and the anchor ball should be at least three times the water depth. The length of the anchor rope Under different sea conditions: In general sea conditions, the length of the anchor rope is five times the water depth; in calm waters, the length of the anchor rope is three times the water depth; under adverse sea conditions, the length of the anchor rope is seven times the water depth.
The size of the anchor ball is determined by the weight of the anchor. Usually, the volume of the anchor ball is 60 to 250 liters. From a safety perspective, to prevent the anchor from being retrieved for too long and affecting the rapid movement of the oil containment boom, a quick-release device, such as a snap ring, is usually used between the anchor ball and the oil containment boom.
During the use of the anchor, there may be situations where the anchor rope breaks or gets stuck. To facilitate the retrieval of the anchor, the position of the anchor is usually marked by a throwing anchor float; when the anchor gets stuck, the anchor can be retrieved from the opposite direction by using the throwing anchor float and the pulling anchor rope. The length of the rope between the anchor and the throwing anchor float should be at least twice the water depth.
6.4 Issues to be noted when using anchors
In the practice of oil spill emergency response, after continuous exploration and research, some guidelines have been summarized and are worthy of reference. First, when deploying oil booms in waters with high flow velocity, it is advisable to drop the anchor first, then deploy the oil booms, and finally fix the oil booms at an appropriate position. In waters affected by tides, flow velocity, and waves, when deploying oil booms, the ropes for fixing the oil booms should have sufficient slack. Besides using anchors to fix the oil booms, objects such as trees on embankments and pillars of bridges can also temporarily fix the oil booms. In some waters (such as rivers), based on the fixed flow direction, an appropriate oil boom can be selected and one end can be fixed for a long time, allowing the other end to move freely. When necessary, the free-moving end can be used to gather the oil-spilling vessels.
Section 3: Failure of Oil Containment Boats and Its Preventive Measures
The failure of the oil containment boom refers to the phenomenon where the spilled oil that is contained by the oil containment boom escapes from above or below the boom, thereby reducing the effectiveness of the boom. After the oil containment boom is deployed, due to various environmental factors and deployment techniques, various failure phenomena may occur. This section mainly introduces the causes and preventive and corrective measures for failure phenomena such as oil spill carrying escape, oil spill leakage, oil spill splashing, boom overturning, boom sinking, and boom structural damage.
1. Entrainment Failure
The phenomenon of oil escape from containment is that oil droplets constantly detach from the bottom of the oil film under the action of water flow and re-aggregate to form a new oil film on the other side of the containment barrier, as shown in Figure 3-22. This phenomenon is caused by factors such as flow and waves. When the flow and waves are in the same direction, relative to the fixed containment barrier, the movement speed of the spilled oil is the sum of the speed of waves and flow. When this speed exceeds 0.7 knots (0.36 m/s), turbulent flow will occur below the bottom of the contained oil film, causing oil droplets to detach and escape with the turbulent flow. Some of the escaped oil droplets will re-emerge on the other side of the containment barrier and form a new oil film.
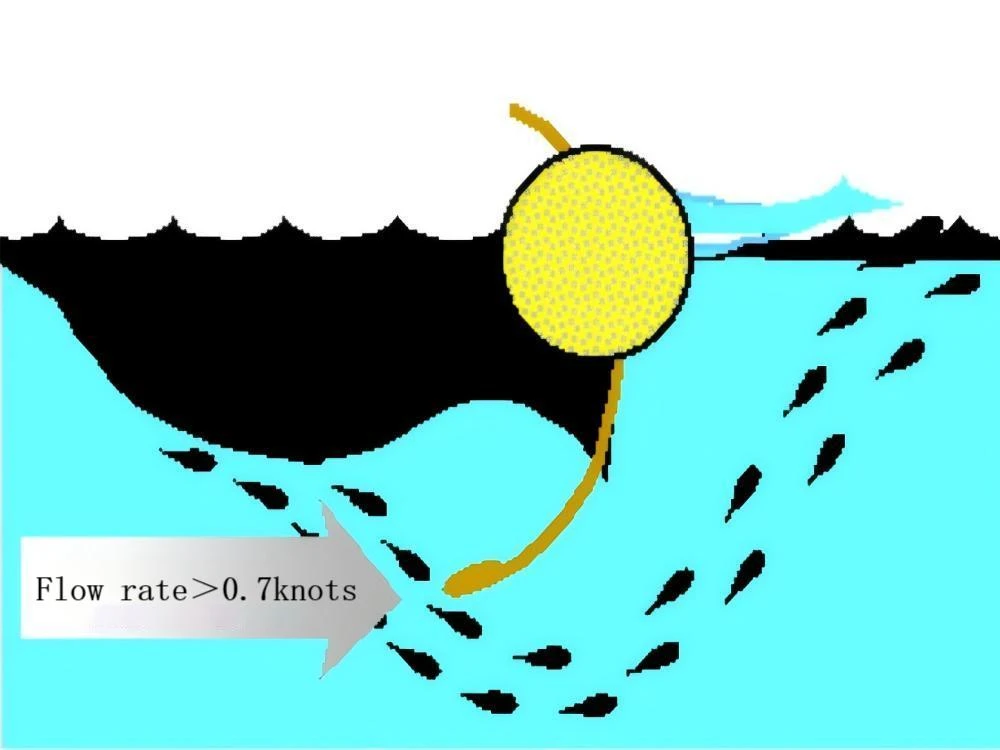
(3-22 Entrainment Failure)
In actual containment operations, the phenomenon of oil spill carrying away is inevitable. To minimize the occurrence of oil spill carrying away, the vertical flow velocity of the oil spill towards the containment boom should be reduced. Therefore, when towing containment booms in open waters, this goal can be achieved by lowering the towing speed (relative to the flow velocity); when deploying relatively fixed containment booms and other containment devices in rivers, the only solution is to form a certain angle between the deployment of the containment boom and the flow direction, thereby reducing the vertical flow velocity relative to the containment boom and guiding the floating oil to the area with relatively lower flow velocity to alleviate the carrying away of the oil spill.
2. Drainage Failure
Drainage Failure It refers to the phenomenon where the oil spill from the containment system spontaneously escapes from the bottom of the containment baffle skirt. As shown in Figure 3-23. The main reasons for this phenomenon are two:
1. If the amount of spilled oil enclosed within the inner side of the oil containment boom is too large, exceeding the capacity of the boom skirt to control the spillage, the spilled oil will escape from beneath the skirt. Usually, compared with the escape of spilled oil carried away by the wind, the amount of oil escaping from the leak is larger. To prevent the enclosed spilled oil from leaking, first of all, it is necessary to promptly recover the enclosed spilled oil using skimmers or other oil collection devices, or deploy oil-absorbing containment booms in the direction of the reverse flow. Secondly, the speed of the boom’s dragging relative to the oil film can be reduced to avoid concentrating too much spilled oil and failing to recover it in time.
2. The shape of the skirt of the oil containment boom has deviated abnormally. The ideal shape of the skirt should always slightly curve towards the direction of containing the spilled oil, forming a slightly curved arc. Otherwise, it is very likely to cause the leakage of the spilled oil contained by the boom. Sometimes, due to excessive water pressure, the skirt may flip backward, resulting in the spilled oil contained by the boom escaping from beneath the oil containment boom. To address this problem, some have attempted to increase the height of the skirt to solve the issue. However, experience shows that increasing the depth of the skirt can only make the problem more severe. This is because the oil containment boom cannot block the flow of water but can only guide the water to flow away from beneath the skirt. The larger the skirt, the greater the water flow speed beneath it, and thus the oil is carried away from beneath the skirt. Practice has shown that the depth of the skirt should not exceed one-third of the water depth.
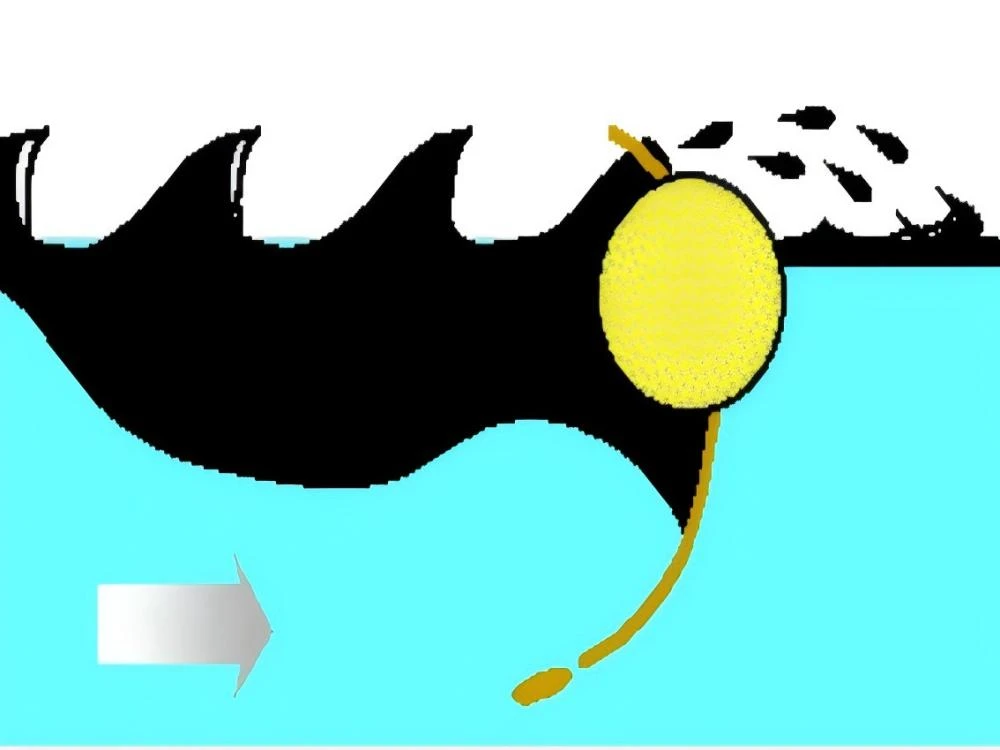
(2-23 Drainage Failure)
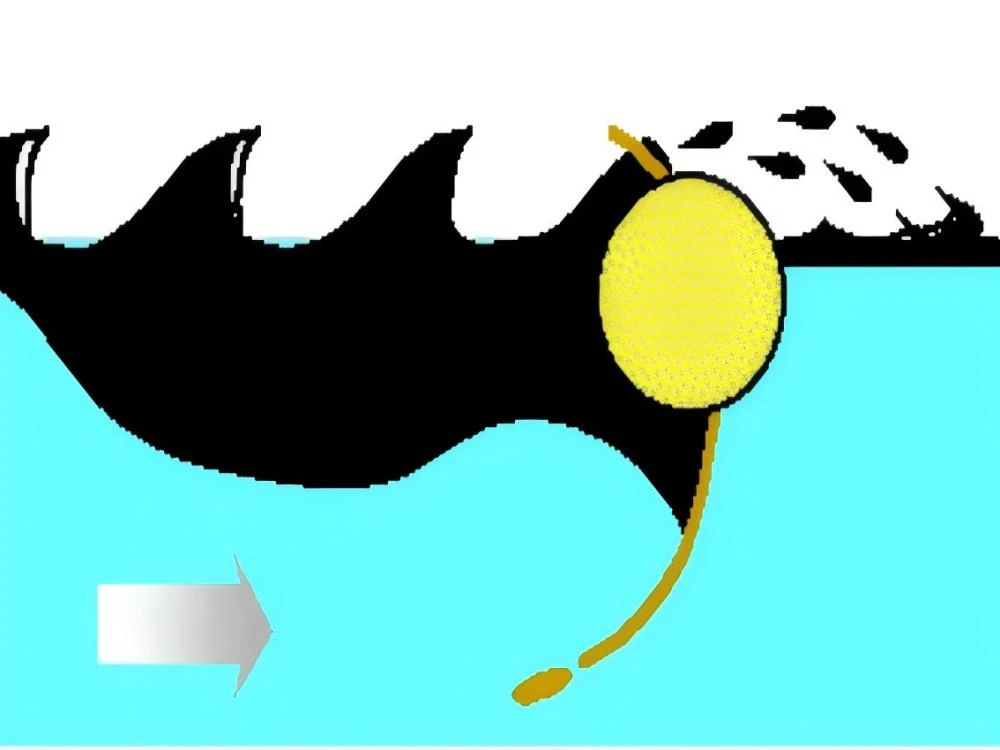
(2-24 Splash-over Failure)
Splash effect failure It refers to the phenomenon where the spilled oil from the containment boom overflows beyond the top of the dry deck of the containment boom, as shown in Figure 3-24. The failure of splash containment usually occurs in two situations. One is caused by the water environment. When the water area where the containment boom is controlling the spilled oil has breaking waves, that is, when the ratio of wave length to wave height is less than 5:1, the containment boom will experience splash containment failure. This situation is more likely to occur in shallow water areas. The main reason for splash containment failure is that the intervals between breaking waves are short, and the containment boom has difficulty keeping up with the rhythm of the waves.
Another situation where splash failure occurs is due to the structure of the oil boom itself. Improper structure can also lead to the occurrence of splash failure. For instance, the lower the freeboard, the more prone to splash failure. Oil booms with a low floatation-to-weight ratio (below 4:1) have poor wave resistance and will experience splash failure along with leakage failure when the wave height is high and the waves are large. To prevent splash failure, a wave-breaking oil boom that can absorb waves should be set upstream of the deployed oil boom. Additionally, when the wave height is 1.0-1.5m, high floatation-to-weight ratio oil booms should be used. This requires on-site commanders to be familiar with the local water conditions, understand the possible wave heights and wave shapes in the actual deployment environment, and select appropriate oil booms based on the water conditions in a timely and accurate manner.
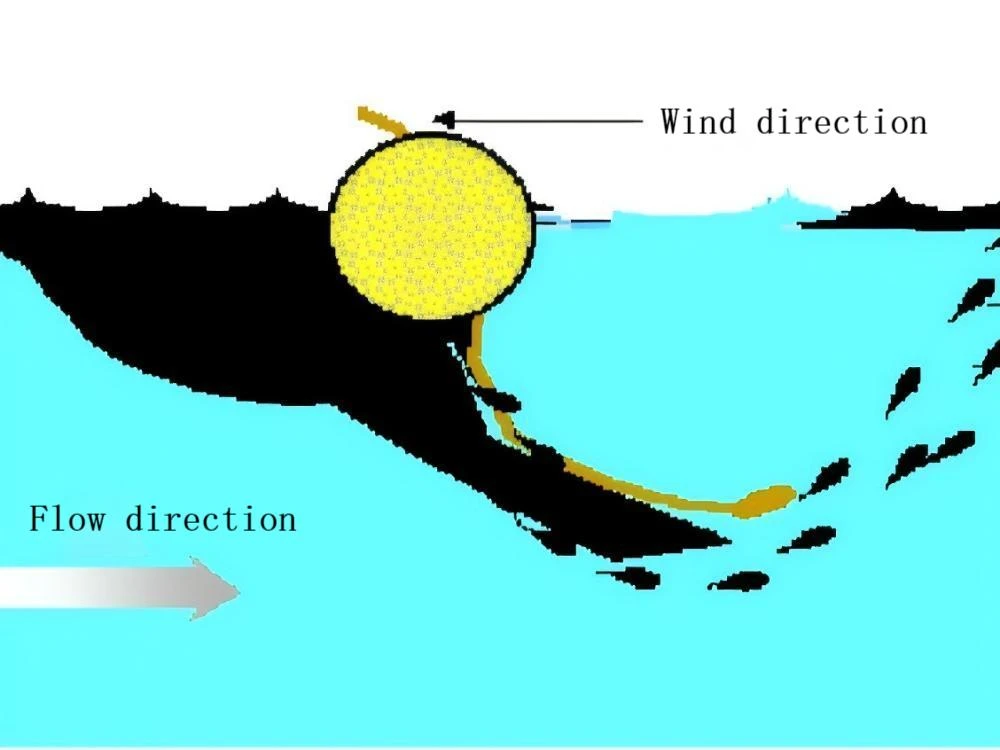
(3-25 Planning Failure)
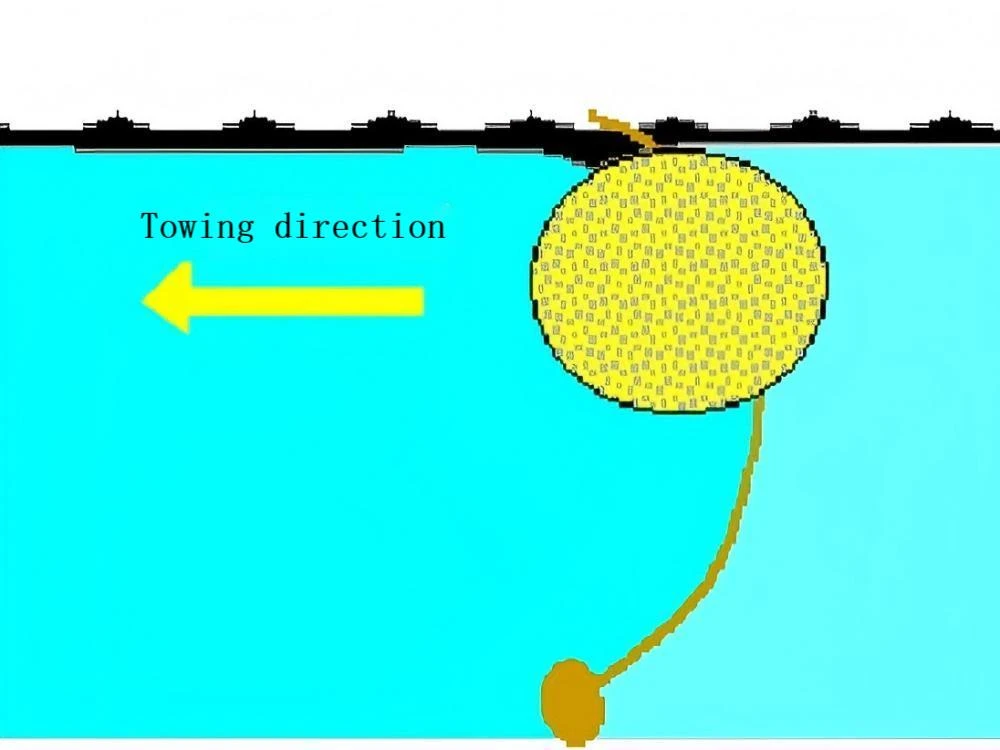
(3-26 Submergence Failure)
4.Planning Failure
Planning Failure It’s refers to the phenomenon of oil spill escape caused by the parallel force acting on the oil containment boom, resulting in the boom tilting parallel to the water surface, as shown in Figure 3-25. This situation mainly occurs because the direction of the strong wind and the rapid current on the water surface is completely opposite, meaning that the directions of these two forces acting on the oil containment boom are exactly opposite, causing the boom to tilt. This phenomenon is prone to occur when the contact area of the oil containment boom with the water surface is too small. Therefore, when selecting the oil containment boom, this point should be fully considered. Barricade-type and curtain-type oil containment booms may also experience this tilting phenomenon.
To prevent the failure of the floating platform from tipping over, it is advisable to consider adding sufficient counterweights on top of the oil containment boom or adopt the method of shortening the counterweight chain of the oil containment boom to keep the oil containment boom in a normal state as much as possible and avoid the occurrence of the tipping phenomenon. In addition, using oil containment booms with a larger contact area with water, such as cylindrical floating bodies, can also greatly reduce the occurrence of such a phenomenon.
5. Submergence Failure
Submergence Failure It refers to the phenomenon where oil spill escapes due to the fact that the oil booms are pressed below the water surface by external forces under high-speed towing, as shown in Figure 3-26. This phenomenon occurs when the towing speed is too fast, and it usually happens before the actual oil containment control is carried out during the process of towing the oil booms to the appropriate position. Another situation is that, if the oil booms have already controlled some oil, leakage failure will occur simultaneously with immersion failure. The solution and prevention method for immersion failure is to reduce the towing speed of the oil booms or to use oil booms with a float-to-weight ratio greater than 10:1. Generally speaking, curtain-type oil booms with a float-to-weight ratio greater than 10:1 can be towed at a speed of 3 knots without experiencing immersion failure.
6. Structure Failure and Calculation of the Forces Acting on the Containment Boom
Structure Failure and Calculation of the Forces Acting on the Containment BoomIt refers to the situation where the force exerted on the oil containment boom exceeds the breaking strength of the materials used, resulting in the damage of the oil containment boom. The forces acting on the oil containment boom are usually composed of the pressure from water and wind, friction, and the vector sum of the shape of the oil containment boom and the wind, current, and wave velocities.
The main reasons for the structural damage of the oil containment boom are: the speed of towing the oil containment boom is too fast (the speed of the oil containment boom is relative to the water surface); the oil containment boom gets caught by protruding or sharp obstacles; the oil containment boom gets tangled by the propellers of the towing vessel; the oil containment boom is too long, resulting in increased friction, etc.
In order to avoid damage to the oil containment boom, during the deployment and towing of the oil containment boom, the following points should be noted: Personnel conducting oil spill containment operations should have received technical training and be familiar with and understand the on-site operation environment; During the operation, strictly follow relevant procedures; Communication should be kept unobstructed, and pay attention to observing whether there are phenomena such as the boom being carried away, the boom sinking, or the formation of strong turbulence at the tail of the boom, etc., and take timely measures (such as reducing the towing speed or adjusting the direction of movement) based on these phenomena that occur.
Section 4: Recovery and Storage of Oil-Flooding Barriers
The deployment of oil booms can be divided into two types: long-term deployment and temporary deployment. Long-term deployment does not have the problem of frequent recovery. Generally speaking, it is the temporary deployment of oil booms that involves recovery, cleaning, maintenance and storage. This section introduces the operation steps and precautions for the recovery, cleaning, maintenance and storage of oil booms.
1. Recovery Operation of Oil-Fighting Booms
The recovery operation of oil-fighting booms is the reverse operation of deployment. The recovery operation of solid float type oil-fighting booms is relatively simple but the recovery speed is slow; while the recovery operation of inflatable oil-fighting booms is relatively easy. The main steps of the recovery operation are as follows:
1. The auxiliary tugboat should first release the towing cables of the oil containment boom to make it operate in a state where it is only connected and towed by the main tugboat.
2. According to the water conditions, it is best for the main tugboat to sail against the current to allow the oil containment boom to unfold in a straight line behind the stern of the vessel.
3. Use the winch or the boom for winding the boom to slowly tow the boom onto the deck or wind it onto the boom reel.
4. During the recovery process of the inflatable oil containment boom, it is necessary to release the gas in the gas chambers while recovering and keep the gas chamber covers well preserved.
5. During the winding process, check whether the oil containment boom is damaged and make records.
2. Precautions during the recovery process
1. During the recovery of the oil-absorbing boom, safety should be ensured. The oil-absorbing boom that has been smeared with oil will be very slippery, which increases the difficulty of the recovery operation and may also dirty the equipment and operators. The deck will also become slippery due to the oil.
2. One person should be assigned to conduct on-site inspections of the recovered oil-absorbing boom and make records. Damaged ones should be repaired.
3. Appropriate amounts of oil-absorbing felt should be available on the deck to wipe off the spilled oil on the deck in time.
4. If the recovered oil causes the deck to become extremely slippery and poses a safety hazard, the operation can be suspended. After appropriate cleaning, the operation can be resumed.
3. Cleaning of Oil Containment Boats
For oil containment boats that are repeatedly used in oil spill containment operations, they generally do not require cleaning. However, if the oil containment boats are used to protect non-oil-spill areas or for shoreline oil spill removal operations and are left idle or stored in the warehouse during the process, cleaning is necessary.
When cleaning the oil containment boats, they should be cleaned using a dedicated cleaning device while being recovered. If there is no dedicated cleaning device, the oil containment boats can be recovered first and then cleaned onshore. However, a cleaning area should be set up to avoid the spread of the cleaned wastewater, which could cause secondary pollution.
Manual cleaning of the oil barrier net should start with gently scraping off the thick oil layer adhering to the surface of the net with a scraper (preferably made of wood). Then, it should be cleaned with warm water or scrubbed with a detergent brush. Finally, it should be wiped clean with an oil-absorbing cloth. Under good weather conditions, 6 to 12 workers can clean the oil barrier net for 305m in one day.
When using the oil barrier net cleaning device, the angle between the spray gun and the surface of the oil barrier net for cleaning should be less than 45°. The water temperature used should not be too high. The lower the temperature is, the better, as long as it can remove the surface oil. Avoiding premature aging of the protective coating of the oil barrier net.
The oil barrier net should be rinsed clean with fresh water, placed in a cool place to dry, and then stored in the warehouse.
4. Storage and Maintenance of Oil-Fighting Booms
The storage and maintenance of oil-fighting booms are directly related to whether a rapid oil spill emergency response can be carried out and whether effective containment operations can be implemented. To ensure a rapid response, the storage locations of oil-fighting booms should be as close as possible to the wharf, the operation site, and the sensitive resource protection areas, and the storage locations should be convenient for the entry and exit of vehicles and ships. For oil-fighting booms stored outdoors, it is necessary to ensure that the drainage conditions of the storage locations are good and to pay attention to pest control, moisture prevention, and avoiding direct sunlight exposure. For those stored indoors, it is also necessary to pay attention to moisture prevention and ensure good ventilation conditions. Depending on the situation, necessary measures should be taken in advance to prevent pests and avoid damage to the booms (such as spreading rat poison, etc.). For oil-fighting booms that need to be folded for storage, they should be placed on shelves and no other items should be stacked on top to avoid excessive pressure causing deformation of the booms. Regularly unfold the folded oil-fighting booms for inspection and re-fold them when necessary, avoiding the original folding marks. If the oil-fighting booms need to be stored on reels, it is necessary to avoid twisting during the winding process and regularly unwind all the oil-fighting booms that are wound to check and then re-collect them. The maintenance of oil-fighting booms mainly refers to daily maintenance and maintenance after the completion of the recovery operation. After the completion of the recovery operation, the maintenance mainly checks whether the booms are damaged, whether the accessories are complete or whether they need to be replaced and repaired; daily maintenance generally checks whether there are damages, cracks, fiber aging, corrosion or damage to the connectors caused by pulling and other loading and unloading reasons of the oil-fighting booms, and performs necessary repairs and replacements; for oil-fighting booms that are long-term placed in water areas, regular maintenance should also be carried out. Generally, according to specific circumstances, the oil-fighting booms should be towed ashore regularly to remove marine organisms and other adhering substances attached to the surface of the booms; regardless of which maintenance and maintenance are carried out, detailed records should be made and inspection and maintenance items should be arranged based on the records to ensure that all contents related to the oil-fighting booms can be comprehensively inspected and maintained within a certain period of time, so that the oil-fighting booms are always in a good standby state.