Jerryborg Marine Foam Filled Fender
Jerryborg Marine uses heat-sealed foam for its fender core. The foam is fully enclosed and covered with a strong, reinforced polyurethane exterior. This feature makes the fender highly resistant to stress, allowing it to absorb large amounts of energy while operating at sea.
Our foam fenders stand out for their consistency and superior quality. Available in five foam grades and both U.S. and metric standard sizes, they cater to a wide range of needs, from ultra-low hull pressures to extreme performance demands. Reinforced with Flosys 4-axis filament winding, they achieve exceptional strength and a uniform finish. The PU elastomer skin features an extra abrasion-resistant layer and is customizable in nearly any color, with black, grey, and orange as standard options. These foam-filled fenders have special insides to prevent overloading and manage docking pressure. They make mooring safer and simpler, even in rough weather.
They are available in various sizes, from 200mm to 4,500mm in diameter and 500mm to 10,600mm in length, and are designed to meet various maritime needs. They also come in different foam densities and shapes. Depending on the specific setup required, they can be installed using a two-point or four-point mounting system.
Place of Origin | Shandong, China |
Brand Name | Jerryborg |
Material | Polyurea coating and solid foam |
Product Name | EVA Foam Filled Fender |
Color | Customers’ Requirements |
Usage | Protect Ship |
Size | Customized Size |
Certificate | DNV, GL, CCS, BV, LR |
Surface treatment | Polyurea coating |
Warranty | 24 months |
MOQ | 1 Set |
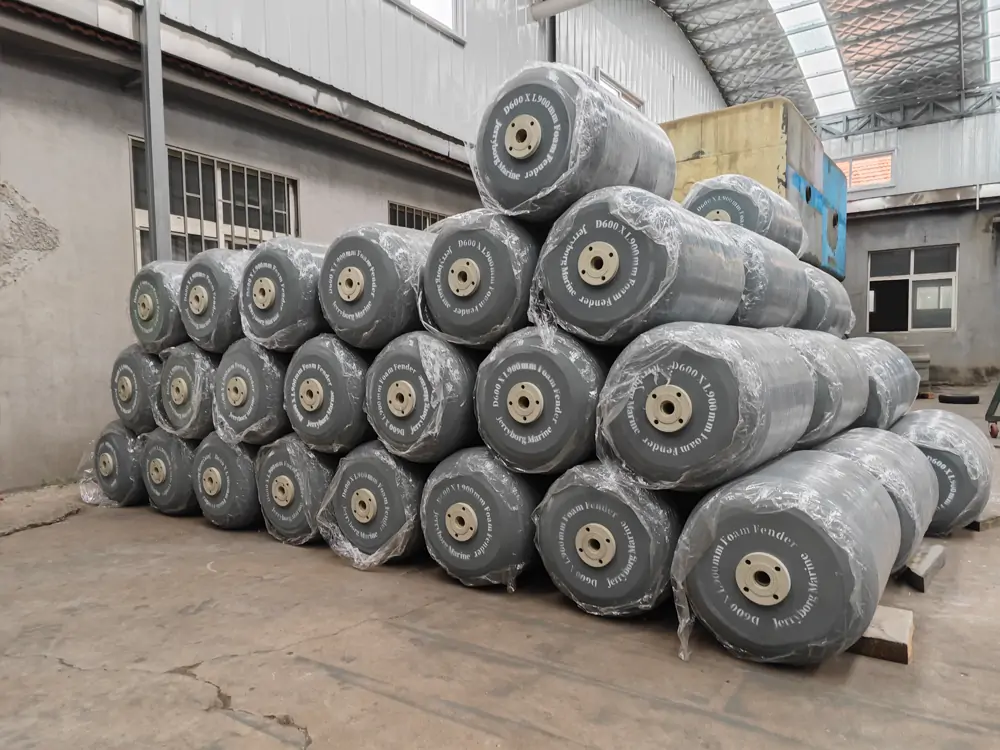
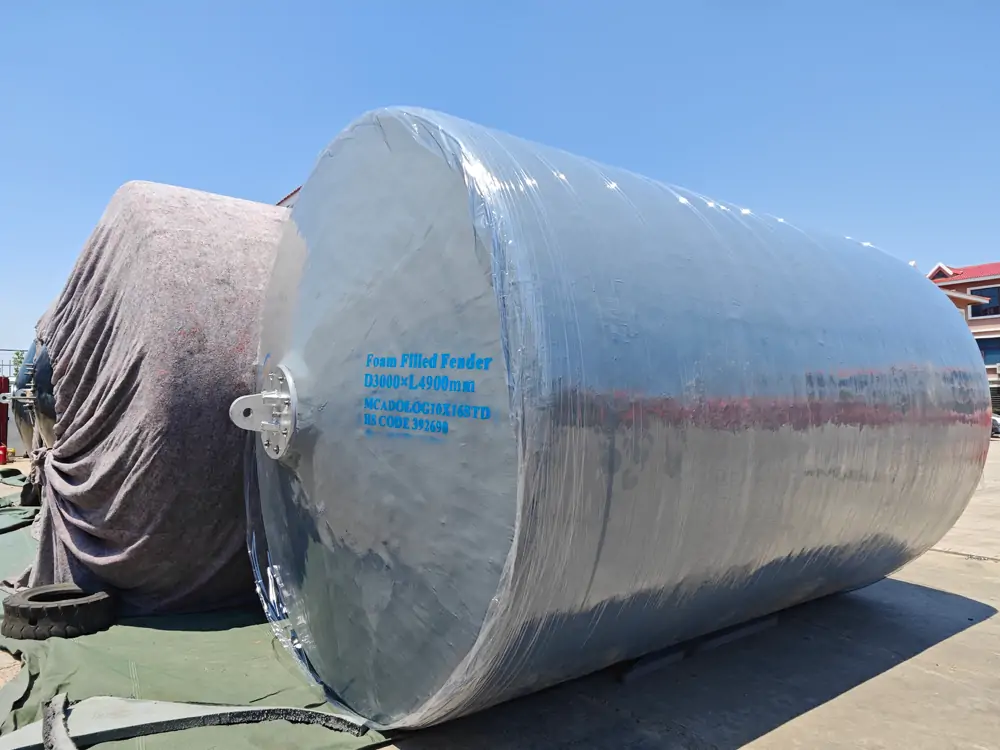
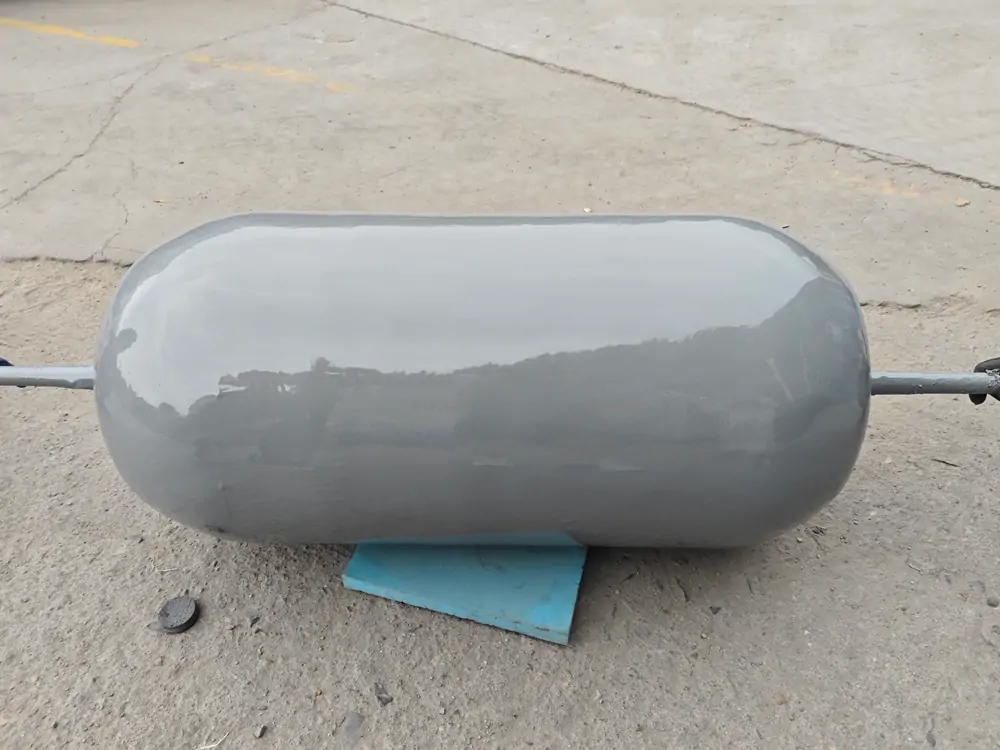
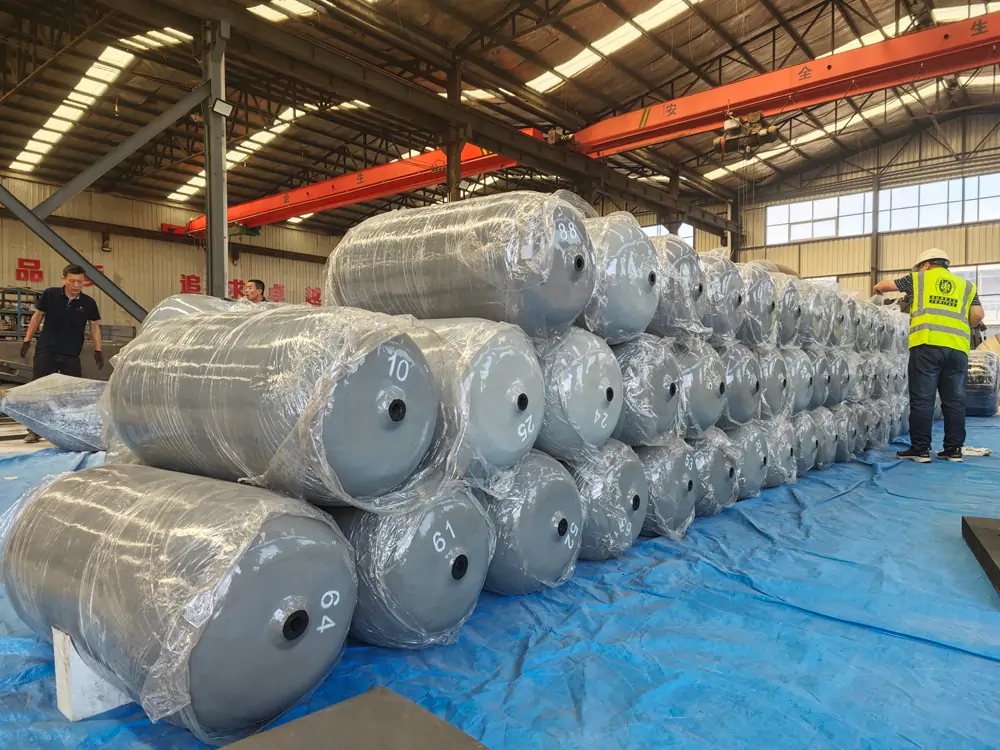